160: ‘Project Phoenix, Part 2: Prefab Modular’, with David Benjamin and Andrew Meagher
A conversation with David Benjamin and Andrew Meagher.
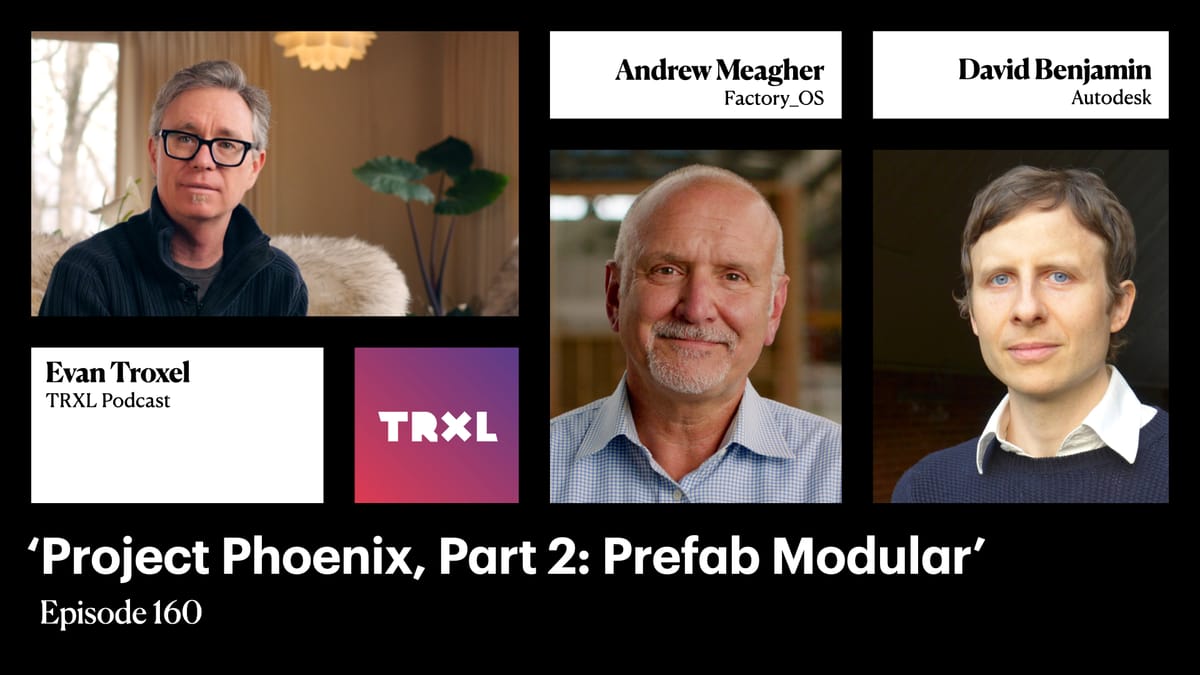
David Benjamin and Andrew Meagher join the podcast to talk about prefab modular and the construction of Project Phoenix in the second installment of a three-part series of episodes on the podcast. In this episode, we take a comprehensive look at Factory_OS's modular manufacturing approach to residential construction and its partnership with Autodesk which aims to create sustainable and affordable housing. Today we talk about the role of data-driven design, innovation throughout all stages of design and construction, and the collaborative approach to address housing and climate challenges with this project.
Episode links:
- Andrew Meagher on LinkedIn
- Autodesk Research website
- Autodesk on LinkedIn
- Factory_OS website
- Factory_OS on LinkedIn
- Project Phoenix Modular Housing Shows a Sustainable Way Forward (YouTube)
- TRXL 159: ‘Project Phoenix, Part 1: Design’, with David Benjamin and Ryan McNulty
About David Benjamin:
Architect David Benjamin leads applied research on Net-Zero Buildings at Autodesk Research. His work combines research and practice, with a focus on an expanded and actionable framework of environmental sustainability. Over the past several years, his team has explored generative design, low-carbon materials, and re-usable design intelligence for the built environment.
About Andrew Meagher:
Though originally from New York, Andrew has spent more than half his life in the Bay Area. His background spans more than thirty five years in the architectural profession. While his early career focused on global retail design and rollout, he has since devoted the last twenty five years to addressing California’s critical housing needs.
Andrew has directed projects across many disciplines, including master planning, mixed use, supportive, affordable, workforce housing, veterans and senior living, and new concept development.
As a founding member of Factory OS and Chief Design Officer Andrew is responsible for the creation of Factory OS’s standardized volumetric designs, specifications and building systems and oversees all architectural & engineering activities. Andrew collaborates intensively with developer design teams, city agencies, non-profits, and community stakeholders through every stage of the process from feasibility through fabrication. He strives to maximize efficiencies that volumetric design affords, while creating thoughtful homes focused on the wellbeing of the resident and which foster environmental stewardship.
Connect with Evan:
Watch this episode on YouTube:
Episode Transcript:
160: ‘Project Phoenix, Part 2: Prefab Modular’, with David Benjamin and Andrew Meagher
Evan Troxel: [00:00:00] Welcome to the Troxel podcast. I'm Evan Troxel, and in this episode, I welcome Andrew Meagher and David Benjamin to the podcast. Andrew is a founding member of Factory OS and their Chief Design Officer. He is responsible for the creation of their standardized volumetric designs. specifications and building systems and oversees all architectural and engineering activities.
As you heard in the last episode, David leads applied research on net zero buildings at Autodesk Research. His work combines research and practice with a focus on expanded and actionable framework of environmental sustainability. Over the past several years, his team has explored generative design, low carbon materials, and and Reusable Design Intelligence for the Built Environment. Today we're talking about Prefab Modular and the construction of Project Phoenix in the second installment of a three [00:01:00] part series of episodes on the podcast.
In this episode, we take a comprehensive look at Factory OS's modular manufacturing approach to residential construction, and its partnership with Autodesk, which aims to create sustainable and affordable housing.
We also talk about the role of data driven design, innovation throughout all stages of design and construction, and the collaborative approach to address housing and climate challenges with this project. We also hint at the next episode in the series regarding the integration of plant based biomaterials in a novel façade panel system.
So before we jump into today's conversation, please do me a couple of favors. As always, if you are enjoying these episodes, please Please subscribe if you aren't already, both to the show on YouTube and in your favorite podcast app to let me know that you're a fan, it really, really helps, and if you're watching on YouTube, please click that like button too, that is a biggie, and if you'd like to get an email when episodes are published with all of the links and other [00:02:00] information about the episode, you can sign up for that at TRXL.co, which is also where you can find every episode of this podcast, including part one in this series.
This was a fantastic conversation with Andrew and David, and I hope that you'll not only find value in it for yourself, but that you'll help add value to the entire profession by sharing it with your network. So now without further ado, I bring you my conversation with Andrew Meagher and David Benjamin for part two of the Project Phoenix series.
Evan Troxel: welcome to the podcast officially.
It's great to have you both here to talk about Project Phoenix today.
David Benjamin: It's great to be here.
Andrew Meagher: yeah, thank you for having us, Evan.
Evan Troxel: Well, let's kick this off with where this story begins on the manufacturing side. And so maybe Andrew, you can kick us off and talk about what Factory OS is and the involvement in the [00:03:00] project. I know you're a Key player in this project and, uh, and then I think that'll lead us into discussion about the partnership with Autodesk to make this a reality.
Andrew Meagher: Sure, um, if I can just briefly, Factory OS is a modular, volumetric manufacturing platform. industrialized construction for residential dwellings. And so we'll do everything from workforce housing to affordable to supportive. We've now branched out into student housing and as well down into emergency housing.
Evan Troxel: Nice. And can you give us an idea of your background and what you do at FactoryOS?
Andrew Meagher: I was on the design side before Factory OS, before there was a Factory OS, and I worked on a first modular project with the founders, Rick Holliday and Larry Pace, and the success of that gave everyone the confidence. They had been looking into opening up their own factory prior, but the success of, the successful outcome of that project really reinforced that [00:04:00] opening up their own factory would be the right way to go.
So we, they opened up a factory here on Mare Island in 2018, and they asked me if I would head up the architecture and engineering department. So I've been with the factory since essentially before there was a factory, and I've been in charge of the specifications, of the fabrication drawings, overseeing design of certain components and assemblies and sub assemblies.
I also work with outside architects and our own production team. Consultants that are, we call them friends to the factory. So as we iterate and bring new ideas, we're able to test it and validate it with
our consultants around us. And just to give us an idea of the coverage area, because I know factories, industrialized construction, a lot of times it's, it's regionally based. So give us an idea of the coverage that you guys provide.
So we're, uh, our coverage basically will go down to, say, San Diego up towards Oregon, and we've looked, we've gone as far east as Truckee and Tahoe. [00:05:00] Once we go further east, our trucking costs start to go up. And the local labor starts to go down. So that's been the limiting factor. We've explored work in Arizona, we've explored work in Texas, and each time it's come back that it wouldn't pencil.
Not to say that that won't change in the future, but those are the limits.
Evan Troxel: I'm a recent transplant to Oregon, Southern Oregon, uh, but you also mentioned one of my favorite places in the world, which is where I grew up, which is in Truckee. And uh, one of the things that always stood out to me about Truckee, cause I, I also lived a lot of my life in Southern California, where the winding roads up to the top of the mountain, very steep switchbacks, tight turns. And in Tahoe, it's not like that. It's like wide open freeways. I mean, there's a grade to it, but they just, and so like trucking wise, I can, you know, bringing this back to where, where you were going, like, you, you actually can get stuff to that region because of logistically, you're not having to deal with extreme conditions on the roads.
I mean, obviously in the middle of winter, we just, I think we just read about [00:06:00] this, you know, it was a couple of weeks ago that they had a giant closure up there because of the storms. But for the most part, it's just like a straight shot. It's pretty nice. Well, you actually bring up an interesting point. So, the reason why Modular, uh, Was appropriate in Truckee was not so much that we were bringing down the cost, although we were, it's that we were able to shorten the construction schedule so that they could build before. So they set the foundations right before winter, knew that winter would come, took a pause, and this was all planned.
Andrew Meagher: And then as first in the early spring, the mods were here, ready to go. And then they were able to build the, the project in
about a year.
And you do speak about the, the winding road. So that was one thing that, cause we built our truckie project. It was like our third or fourth out of the gate here at the factory. And one of the things we wanted to confirm is that if we installed the windows here at sea level, that when they went up and over the mountains that, you know, whatever thousand feet that it was, that there wouldn't be a pressure differential that would then affect the Argonne gas and whatnot.
So we worked closely with the manufacturer to make sure that
there wouldn't be any issue and we [00:07:00] were fine. And then from a
Evan Troxel: Because you're going from zero elevation to 70, 200 feet or seven. Yeah. Like Truckee's pretty high up there. So
Andrew Meagher: And then, uh, from a trucking perspective, the logistics were fair. I will say they were fairly straightforward. You know, we, we give our different trucking companies, our location, the destination location, they'll project a route and tell us if any closures need to happen or if there's a escort vehicle or a pilot car or whatnot.
And it was, I would say it was pretty standard for what
we do for most of our product.
Evan Troxel: I'm sure we'll talk more about logistics as we get into this conversation, but I, David, you've been incredibly patient. Thank you so much for the extended intro there. Uh, but I think it, it's great to kind of set. Set a backdrop for the conversation today. So, David, please, uh, introduce, uh, the project from the Autodesk perspective, and I know there was a partnership early on, on the Project Phoenix project.
So maybe you can just tell us a little bit about that.
David Benjamin: Yes. Sounds, sounds good. And, and by the way, I, I always [00:08:00] love, um, hearing Andrew talk about anything, so I'm glad to wait here.
Andrew Meagher: Well, likewise,
David.
David Benjamin: but, uh, so, um, you know, I think Autodesk, um, saw the benefits of, industrialized construction and the work that Factory OS was doing pretty, pretty early on. And Autodesk became an investor in Factory OS, um, several years ago.
And I think there was a kind of shared idea that all of the spirit and practical innovations that Factory OS was doing to make housing more affordable, constructed quicker. In a super scalable way and also sustainable, you know, are things, you know, those are things that shared in the, in the vision between FactoryOS and Autodesk and really trying to demonstrate what's possible to [00:09:00] raise the bar for the entire industry.
Um, then I think probably Andrew, it was about a year and a half or two years ago as the relationship developed and, um, you know, between Autodesk and FactoryOS. Um, we saw the potential opportunity to really test out, um, some new ideas, some ways of pushing the limits of what had been done before to test that out on a real world project that you at Factory OS, um, and your development arm had been, you know, figuring out, you know, that, that we're now calling Phoenix.
And I think that really allowed us to kind of. Supercharged some of our more direct collaboration and work together, you know, and, and I've always learned best by, by doing, you know, project based learning and I, think, this
Andrew Meagher: most do. I have to agree with you. Everyone here at the [00:10:00] factory, we, we learn by doing. And we don't, we
don't hesitate to do.
David Benjamin: yeah, exactly, and you're a great model in that. And so we thought, hey, together, let's, let's actually.
See what we can, we can do together, you know, in this, in this real way, but also I always appreciated Andrew that, that you and, and Larry and others at Factory House thought of Phoenix as an innovation village. It's like a real world place where we're going to try out some of these innovations and we're going to, we're going to see if we can move the needle a little bit.
And, and that's super bold. I mean, you, you know, I've, I've. I've worked as an architect for a while now, and you don't always get the, the project and the client who's willing to say, let's treat this as a, as an innovation. Let's do some things here for the first time that haven't been proven out before.
And so that was especially exciting for me to work with, to work with [00:11:00] you and the team on that.
Andrew Meagher: and I think it was exciting for all of us. I mean, you, you did hit upon something that, uh, Autodesk and Factory OS, our values were aligned, you know, in, in a really substantive, meaningful way about lowering the cost of housing and who we're trying to lower it for. So it isn't just, let's bring down the cost of housing and if it's luxury housing, so be it, like, like we don't, we don't care.
It's, we come from a background of wanting to do affordable, supportive, you know, uh, housing for, and workforce housing. And then also where we could, to be more sustainable. And the Phoenix site was actually acquired, I want to say about a year or so prior to when we actually opened up the factory. So, We had it in mind that it was going to be some sort of modular development.
But at that time, if we made it just a modular development and we were done, we were thrilled. So when along came the introduction to Autodesk and the introduction to [00:12:00] your team, and the idea that we could make it this innovation village and actually have test out ideas amongst ourselves, We were very excited by that.
That was something that was brand new, you know, brought to the, brought to the effort we thought would definitely have a significant and a positive
outcome.
Evan Troxel: The idea of Project Phoenix. Coming to fruition through this kind of, uh, prototype, iterative, but then very real project is a really great story. And at Autodesk University last year, we got to see one of the modules on display along with a lot of other kind of supporting elements, including, you know, technology that, That went into it, but also materials.
Um, and then there was, like I said, a module there that we could walk inside of and actually see the output of the factory that gets shipped to the site. And I love the idea that there's actually, this is where the rubber meets the road, right? This isn't [00:13:00] just something we're talking about doing, but this is something we're actually doing. And putting that on display, I think, as you said, David, to inspire, to raise the bar, to inspire other people to show it can actually be done, but not everybody has a partnership with Autodesk, right? And, and to raise the bar, you, you really do have to take what you're learning as Factory OS and Autodesk and put that on display so that it, it raises the bar.
all boats. And so I'm curious, David, kind of what Autodesk's approach here is when it comes to that, because I know that that that's kind of an ethos of the company as well. And, and, uh, a previous guest on the podcast, Kian Walmsley said, you know, Autodesk likes to take 100, 000 technology and turn it into 10, 000 technology.
It's like some rough numbers, right? And make it available to a lot more people. And so I'm curious, is that if that's the same thinking with industrialized construction.
David Benjamin: Um, yeah, definitely. I mean, so, Um, I think [00:14:00] the, the, the idea is, is always, you know, with the things we're doing research on to try to prove them out, you know, in a kind of tangible way as the, the first time doing it, but always with an idea to, could this be generalizable, you know, to many other buildings, to many other projects, um, and, and even to, to many other, you know, Parts of the world and types of, you know, design professionals and engineering professionals, construction professionals.
Um, so, so I think this, this project and our work together, you know, followed that, that same general path. Um, I want to maybe take a quick step back and say that, um, you know, the, the, this project, like some of our other research has aimed to, like, think about some of the most, um, The biggest challenges, the hardest things to solve, um, but [00:15:00] also demonstrate them practically.
And one category of this, I think, was the housing crisis. And, Andrew, you're always so eloquent in describing the details of the housing crisis in California. Another aspect was the climate crisis. And that's something that, for me and my team, we've been working quite a bit on over the years. And so Um, I can describe a, a, a little bit more about some of the generalizable insights that we, and tools that we tried to create on, on this project, but I think it's helpful to understand that, that context.
Um, maybe, Yeah,
Andrew Meagher: Yeah, so, I mean, that is actually one of the motivators behind, The factory and why we felt we now is the time. There's a housing crisis that's been building in California for probably 30 or 40 years, depending on who you ask and, and, and how we got there. Right. So we've had a significant population growth.
So that's a factor, [00:16:00] but we also put policies in our way. that blocked and slowed down the ability to build housing. And I'm talking just from a planning department decision, let alone building code and title 24. And all these, all of these things are good, uh, to have in place. You want to have energy efficient buildings and whatnot, but they drive the cost up.
And then with fluctuating interest rates, you, you have fewer and fewer who are willing to take the risk to actually build. Then you couple that across the whole country. I think the number is about, there's a shortfall of 7 million homes in the U. S. at this moment, and I think, and you could, depending on who you, ask, you know, at least a shortfall of two to two and a half million homes in California alone.
So we're not going to conventionally build our way out of that problem. The, the, you can't legislate and say, okay, we're going to take off the guard rails and go ahead. Everybody just stick build until we're done. with industrialized construction, that's going to be one of the mechanisms, [00:17:00] one of the ways where we can start to have an impact.
It won't be the only way, but if we can start to build, and we are doing this now, two and a half to three homes a day out of the factory, scalable up to four to six homes at, uh, sorry, Two, two and a half to three mods a day, which is six dwelling units a day. So we, we're, we'll be able to do six, currently we can do six.
We can get up to eight or ten very easily within a, a day shift in just adding some tech, uh, some technology. Then comes in standardization of our specifications, standardization of our assemblies and sub assemblies, and truly that did take us a number of years to get there, to really find out. what works from an acceptable standpoint in the marketplace to what is a fast build on the factory floor to what is an optimization of the materials that we have coming in.
And now we're at a point in every six months our company is It's different because we're constantly [00:18:00] evolving and improving, bringing on new expertise and working with Autodesk on software that will, you know, help give guidance to that. And it's, those are the kinds of advancements
that are needed.
David Benjamin: Yeah, and it's
Evan Troxel: I'm going to steal some, I want to steal some words from you. I heard you say this before too, like, like Andrew spoke to the scale of what needs to get built 7 million homes and, and stealing from you with, we have to do that with zero carbon, right? So I would love it for you to, to jump into that side of it as well.
Yeah.
David Benjamin: um. We've got these different axes of the problem. So we've got the, the housing crisis and the climate crisis. And I'll, I'll talk a little bit from my perspective about the climate crisis in AEC in just a sec, but also I'm, I'm just thinking now we also have these components or this axis of like the physical innovation that we need and the digital innovation that we need.
And so this project kind of brought together all of those things, [00:19:00] you know, across, across those different axes, um, you know, with obviously FactoryOS being, doing all of this incredible stuff with the, the physical innovation, um, figuring out how to get that assembly line going and get all of the efficiencies of the factory built housing.
solve all the details, do the production, get the supply chains right. But then there's also this data layer and there's the digital layer. And we worked on that together in this project, another area where we have a kind of shared vision. Um, but back to the, the climate crisis. I mean, I've just been thinking for a number of years now about this kind of impossible set of numbers, uh, you know, which starts with You know, the very real and urgent goal of reducing global average temperature rise to 1.
5 degrees Celsius. I mean, that's what, when you hear people talk about science based [00:20:00] commitments and the Paris Climate Agreement and the United Nations, we're talking about 1. 5 degrees. Okay, so to get to 1. 5 degrees, we need to reduce carbon emissions. By about half by 2030 and basically eliminate them entirely by 2050.
Okay, so that's, that's a challenge in itself. Then at the same time, in exactly those same, about 30 years, you know, that we need to get to net zero, we're expected to double the built environment, take all the flower area you have today. and double it. I mean, it sounds crazy, but it's partly because of population growth and urbanization.
Some of the same things that are, that you mentioned, Andrew, that are driving a housing crisis. Um, and it, it basically translates to the world needing to create a New York City's worth of buildings every month, you know, this month, next month, the month after, [00:21:00] or another way to look at it, creating, you know, building, 13, 000 buildings every day.
So today, 13, 000, tomorrow, 13, 000, the next day, another 13, 000. So how can we possibly, uh, quickly get to net zero and at the same time, quickly, you know, build this many buildings. It's, It's, it's a huge challenge and what, what it, what it really means to me is we can't get there by incremental improvements.
We can't take the way we're doing things now. This is my version of what you say, Andrew, about stick build. You know, we can't just take the way we're doing things now, which we could say is the same as stick build, and just incrementally make it better 5 percent a year or some years we get 10%. We just don't have enough time to do that and still hit our marks.
So we need really radical transformations [00:22:00] in our physical world, in our digital world, in the way we're approaching this, in the speed of construction, in the cost of construction, in the carbon footprint of construction. We need reductions of carbon by like half. We need to be making stuff that's half the carbon emissions of traditional, and eventually Getting to zero or negative.
And, and so that's the kind of ethos that, that me and my team brought in. And that, you know, again, we found kindred spirits in, in the factory OS team of saying like, Hey, can we, can we really try to go for those goals
Andrew Meagher: And I think, David, the other thing, though, that was also key to all of us was the idea of habitability and that you're truly creating homes and communities and your designs are going into existing environments. So, it's one thing to say, okay, we've got to house this many people, we're going to build umpty dumpty buildings, they're going to be this tall, and we're going to shove them in there, and we're going to be done, and we're going to claim victory.
You know, that's a nightmare. That's a nightmare scenario. So [00:23:00] now, how do you then say, okay, we're going to do these other goals while hopefully improving habitability, making it better for people, knowing that they're going into sites that are a lot more challenging acoustically, environmentally, uh, you know, from a configuration standpoint, these aren't greenfield site opportunities.
A lot of these are either in urban areas, We're close to urban areas. And so we're pulling all of that challenge together. So what about daylighting? What about acoustics? What about views to the street, to the neighborhood, to, um, connections to it? Maybe if there's a park or a courtyard. So now we're going to do that.
We're going to look at cost. We're going to look at carbon and we're going to look at speed. If you took the best brains that the industry had to have, that is months worth of drawing, and iterating, and rejecting, and guessing, and presenting, and then [00:24:00] hoping that people believe you, and so, working with Autodesk, week after week, we would Turn out, you know, options, and they'd say, if we had software that looked like this and could computationally compare these things, analyze them very quickly, are we headed in the right direction?
And so that's what our collaboration was really about. So, you know, builders on our side who could give a thumbs up and thumbs down, expertise on their side from software and carbon analysis, and really start to create something
that could be shared at scale.
David Benjamin: Yeah. And to get back to one of your questions, Evan, like, so what, what What is, um, how do, how do we scale up some of the software side? You know, um, we really wanted to do those, those exact things that you were describing, Andrew, which is sometimes I describe it as like, um, you know, it's important in, in almost any project.
So this is the generalizable part to [00:25:00] be able to simultaneously look at things like operational carbon, embodied carbon. But also cost and also livability, which is a huge category. Each one has subcategories, but managing that complexity is difficult. That's one place where computers can come in and, and really help us.
There are many constraints of a site. There are many goals and sub goals for different projects, including these carbon cost and livability. How do you, you know, rapidly explore a lot of design space? And come out with designs that are, that are achieving these outcomes that, that you and the state, the whole stakeholder team has wanted that.
That's more or less true for housing. And this was true for Phoenix, but it's also true for other building types. And it's true, you know, in India as well as it's true in, in California. So we, we learned a lot from the specific [00:26:00] project, but then ma, you know, are aiming to make that very generalizable. To many other projects, even beyond housing and even beyond California.
Evan Troxel: And you guys are really speaking to a process change or a workflow change on so many different levels. Uh, we, when we look at the traditional practice of architecture and engineering firms and then handing off to construction and different delivery methods, a lot of times those are kind of trustless, uh, in those processes, right?
Because it's like we were, we're avoiding all of this risk by just, just looking at the things in our blinders, right here, what's right in front of us. And we're going to hand, we're going to throw that over the fence pretty much literally to have somebody else look at it and take it to the next level.
Or maybe there's a little bit of back and forth through a very contentious process of submittals and RFIs and change orders. And, you know, we, we've all been there and, and, and experienced that. But you're talking about having. Key players at the table at the same [00:27:00] time, early on the project, with a common set of goals, right, which is those outcomes, this kind of outcome based design that you're really going for, I think is a key driver for that, right?
It's because you're, you're looking at the end, and then you're trying to figure out how you're going to get there together. To, to achieve all those benefits and you have a lot of that logic kind of hard coded into the analysis engine, if you will, um, as you're kind of iterating through different design options and, and weights of, because Like you said, it's kind of hard to even maybe put metrics on quote unquote livability, right?
And so you said there's several subcategories in there, which I assume all kind of get different weights and you're kind of making adjustments and saying, because it's all a game of trade offs along the way. We know that, right? And so there's cost, there's carbon, there's livability, there's, there's all, there's the site, there's the environment.
Uh, right, there's all these different things kind of playing a big [00:28:00] game of tug of war, uh, to, because you can't, you can optimize as much as you can optimize for all of those factors happening all at the same time. And to your point, Andrew, like that, the traditional way of doing that takes a very long time to do for a very small number of options, right?
And so when you're layering in the Autodesk Research side of things and Autodesk Forma. and there's other players in the market on the feasibility side as well who are doing a really great job with this. But, but there's, there's this kind of new way of working. It's a new workflow. And I'm just curious from your point of view, Andrew, adopting that workflow, like seeing the benefits of it now that you've gone through it, adopting it is hard enough, but then actually committing to it and going through it.
Can you just talk about the benefits of what you saw happen throughout that process? Because I think part of inspiring the next versions of this for other people to pick this up. You also need to talk about that side of it [00:29:00] because it's not just like, Oh, just flip on the computer and it does. It's not that easy, right?
You actually have to make a lot of adjustments to your organization to even adopt these new ways of working.
Andrew Meagher: Yeah, and so a couple of things, at least. First, if there's an output, you want to know that you can trust it. And so that was one of the things working with Autodesk and us as a factory, and this context is important, is that if you went out and tried to do that on a stick built project, you were analyzing it as a, as a one off.
Mm hmm. And your data input is very difficult to get. It's nearly impossible because nobody tracks it. But at the factory here, we know absolutely every single product that is coming into the factory, the crew that is required to build it, and then what our waste is, our leftover, and what we do with that.
So when we create a volume, or when we were doing these different options and studying it, Autodesk was able to take our Revit models that truly are fabrication [00:30:00] drawings to a very high LOD. Every single stud is accounted for. Every single floor joist, every single sheet of drywall. So, and a waste factor.
So that output is of a high fidelity. So now we've got that level of certainty, we can then start to use the software and iterate and then have outcomes. and Larry Pace's construction experience. He could look at a simple, look at one of the sites, you know, have an L shaped building and five smaller buildings or five stories or four stories or what have you, and he will be able to say, okay, what did you say the construction cost was going to be on this?
All right, hold on. Let me come back. Yep. You're close. Nope. You're off. Something's wrong with your model. So we were able to iterate in that regard. What's we love about it. But I think any user. would benefit from is you have a higher degree of certainty and as a designer to have that kind of power where you're taking out some of your own guesswork and hand wringing because you're [00:31:00] hoping something's right and that when you go to present to a planning department or to a neighborhood group, those neighborhood groups, it's really, we live in a very contentious, difficult environment.
And so you, Historically, you'd go and you'd present and you'd say, well, it's going to bring daylight and we're going to have a park and we're going to improve acoustics and people, you're going to do a shadow study.
Evan Troxel: It's all going to be brilliant. Everything's going to be perfect,
Andrew Meagher: and, and people have to believe you. And I can tell you, having been through those presentations, most don't and it's really difficult.
So now to have a tool where it's objective and you can present it and you say, this is the data. that we found, and this is what we understand we can do. That is a game changing, level raising, uh, approach, and I, I think that's where the strength of all, but, but besides having real world data, if you're a developer, knowing, you know, hey, this is what my habitability is going to look like, and the reason why habitability is important, not just for the community, but if [00:32:00] you have your occupants that want to live there longer.
That improves your proforma from a rental standpoint and people who live there longer then create a community because they get to know their neighbors. And so it's a self fulfilling building prospect. So from a developer, from an investor, from a neighbor, stakeholder, to a planning department giving approval, to the architect doing the design.
These tools are hopefully used in the right manner, are going to be
very powerful and exciting.
Evan Troxel: Well, there's a lot of baggage in this side of the building industry, right? We've all, everybody knows about the quote unquote projects because of everybody can point at a bad example of construction that has turned into a really terrible part of the city, right? And, and these buildings end up getting torn down because they, they, to speak to your kind of long term renters and.
becoming a community, like that didn't happen. That actually happened in the worst ways possible. It became, became a terrible place to [00:33:00] be compounding on that. You're talking about these underserved areas where these projects are going to go. And I don't mean projects in the quotes anymore. I just mean like new projects, right?
And we're talking about leftover area that's between the tracks and the freeway. That is really hard to build on because of all of the environmental constraints, the noise, the, the pollution. Um, and so now we're, we have to figure out ways to build great developments in these underserved and difficult, challenging sites.
And, and the only way you're going to be able to do that is to reassure people through ICANN, through that objective data story that you're talking about. So, so David, I, I'm going to throw this over to you. Like, where's the data coming from that's driving these analysis? And, and because I think part of it is, we also have to reassure the design teams that are going to be using this, that yeah, it actually is trustworthy.
Where's that coming from and why can't, why can they trust it?
David Benjamin: Yeah, I mean, and those were great, [00:34:00] great questions. And, um, but, but I want to first return to something that, that, um, that you were saying, Andrew, it makes me think that, you know, we also shared this vision for, for this project, you know, from the beginning and through our, you know, various collaborations and work together, that the technology, um, is not going to be a magic button.
It's not just going to do everything for you, that the best technology is going to augment your human creativity and intuition. Um, it's going to automate some things, but it's going to free up your time to do other things. It's going to be interactive. So it's going to allow you to, you know, tweak the building a little bit this way and see what the results are, or see if, if you, you know, make that L shaped building.
you know, a right angle, how much sound does it let around the outside corner versus, you know, uh, you know, uh, a lesser [00:35:00] angle. And so we want it to be a very kind of interactive process. And, and, and that's partly the direction that a lot of Autodesk software has been going and that we worked on in this, this project, which is giving you like almost real time feedback.
on anything you're doing on a number of different metrics. Um, also allowing you to compare multiple metrics at the same time. So to see if I'm making a change, not only what is my score for the amount of noise reduction I'm getting, but also what is the carbon score? What is the cost score? What is the, you know, energy footprint of this new design?
So seeing all of those things at once. in a kind of dashboard in kind of real time. That's part of the vision that I think we shared there, allowing you and your team to do the work more quickly, more creatively, deliver housing that's not [00:36:00] cookie cutter, that's not, you know, recognizably second rate as a housing
Andrew Meagher: Right. I don't think any of our expectations or goals were we'd have this sort of wheel of decision making and that you just slide the levers around. And then when you were done, you got a product and then all you had to do was go build it. It was definitely a tool for evaluating different options at a sophisticated level within the input saying, okay, this, this gets us so far, but we know these other things.
And we're going to change the geometry, work on the facade, work on the volume of the building and setbacks and whatnot at a more granular design
level.
David Benjamin: Yeah. And then, sorry, Evan, I didn't fully answer your question yet, but the data, um, comes from different places for different things. So, you know, for, say, daylight, that's based on algorithms that have kind of been vetted over the years. And, you know, people are pretty confident about those. Um, noise has been a little more difficult, but we've been kind of building, [00:37:00] uh, you know, the algorithms around that and validating with, uh, Physical tests and things like that to get that, you know, uh, on par where you can trust the, you know, results coming out of that real time simulation.
But there's another level of data that I think is really important. And this is another thing that we explored, Andrew, for this project, you know, back to when you said, you know, you're already a factory and a shop and developers that, you know, these modules down to every, you know, stud. In the module, you know everything and you have data for that.
You have these really detailed Revit models. Um, one thing that we worked on together was what if in the very early stage of design, when you're just looking at a site and you're trying to figure out what can fit there. What if instead of the typical thing in software, you have to start with the kind of generic box and you're [00:38:00] extruding some shapes and, you know, maybe bending some angles and, um, and then later you might have to say, how do I fill that in with my, the things that I'm actually building?
So instead of that, could you, from the very beginning, say, I know what my building blocks are. I have, you know, unit type A, unit type B, unit type C, and I'm making my project out of these, you know, building blocks. So anything I start drawing is going to be composed of those building blocks. That's another level of kind of design intelligence informed by some versions of AI that allow for a quicker, more relevant type of early stage design.
In addition, something we experimented with was saying, Andrew, you not only have these, you know, different types of mods, and we're going to compose everything out of those types of mods, because we know you're never going to make something that's not out of those mods. [00:39:00] Um, but also, you know some types of designs that have worked well in the past.
And those are made of, you know, of certain types of mods composed with different adjacencies and rules of how high you can go and which ones go next to each other, which ones go on the corner, et cetera, which ones, you know, are single loaded, double loaded corridors, et cetera. So rather than, and you know, this has been a previous version that I myself have worked on in the past, try to encode all of those rules.
That's possible. And that could be really powerful, but it's pretty time consuming to like, you know, The yellow mod always has to go, you know, on the edge, you know, the purple mod has to go next to, or
Evan Troxel: And you have to think of all the exceptions, right? You have to think of all the
David Benjamin: yeah, and you allow
Evan Troxel: coding all that in is hard.
David Benjamin: so it's hard to code it in, but, um, and, and kind of no surprise because of where technology is headed.
Now you can take a few example [00:40:00] designs that have a bunch of logic built into that, even though that's not named or. Algorithmically programmed. We just take some example designs and then basically train a version of AI to generate new designs that are like those designs that you've created. So it's, it's like a lot of the generative AI.
It's learning patterns based on data. And then the system can start creating designs that are more like, you know, the factory OS way to do things. And we think that's a really interesting and powerful direction that not only are we going to compose your designs out of your building blocks, but we can compose your designs in the way that you tend to compose them before.
So we're not just making random,
Andrew Meagher: But building on the
David Benjamin: know, assignments, but we're building
on the successes.
of what's happened before. So these are way, and it's a long answer to your question, Evan, but that's [00:41:00] another type of data that we're looking at using more and more, which is. Past successes as data that we can use specifically for this type of project based on what we know you're working on.
And again, that was very specific for Factory OS, but that can be generalized too. Every type of project, every design firm has some of their past successes. And so can we, you know, create software that learns from those successes and creates designs more and more like that.
Evan Troxel: That's an important point because one of the things that you are, you're, you're not starting from scratch. You're not starting from a blank page. And maybe, Andrew, you can talk about factory OSes. Uh, like, like how many different modules you've, you've gone from your catalog. Let's talk about your catalog and maybe where that's been over the years, because that's, uh, it's again, it's a very important point because you can then take this very strict set of, this is our inventory and use [00:42:00] that as the basic planning blocks instead of saying they're just generic cubes.
Andrew Meagher: So, you know, our factory, we opened in, um, May of 2018 and we had four projects that came in. We had a commitment with Google. Four different architects, four different structural engineers, four different MEP. Every one of them coming to us saying, we, we know modular. And so as we started to build those projects, everyone had a different detail, a different assembly, sub assembly, configuration of what they thought was a good build.
And. Most of the time I would say that was true, but the inconsistency that we were hit with made it almost impossible for us to get any, any meaningful data out of that. It truly took two and a half to three years of working with people and taking baby steps, learning from, I'll say, and learning from the marketplace what it wanted.
Although I will say that, you know, Rick Holiday [00:43:00] came with 40 years of development and I've got 25 years worth of architecture design in the multifamily space. So we weren't ignorant on day one, but trying to then land on something that was truly going to be a marketable unit that you could then turn around and bring back to a client and say, will this work for you?
That was when it started to present that really in 2020. And we gained a little bit of traction, but we were still seeing architects coming to us with pre designed projects. And they'd say here, turn it, make it modular friendly, make this. And that really only worked so well. 2022, 2021, 2022, we actually, cause we do our own developments.
We had a number of projects built that clients could now walk in and see. And go, okay, yeah, I do want this. This will work. This is a construction document. If you will level, it's a product, it's a product with a price and we understand everything, every [00:44:00] aspect in it, and it's in Revit. So now we're able to, we go back to the marketplace and we have a couple of dwelling units.
We have about 27 different types of dwelling units that vary from, um, an efficiency dwelling unit to a, uh, studio, uh, urban one, we call it a borrowed light one. A true one, a two, and a three, and then we have some iterations with it's a three bed, two bath, that kind of thing. So we have all of these dwelling units, productized, we know everything about it.
On a day one, we can start the conversation right there, and then they can react. And they can come back and say, well you know what, if those urban ones, which are small, if you made them four inches wider, We would get better usage of the site and they'd be more habitable. Tell us how feasible is that?
Well, now we have all of our, our, our trust framing, our joists, our cast iron. I mean, this is a little boring stuff, but it's, it's [00:45:00] very impactful. And we can come back and sometimes a matter of hours. Now, even used to take a week or two. We're now down to hours and coming back and saying, yep, four inches wider.
It works. This is what you get. This is where we can put it. There is, you know, the cost change is minimal. Um, you know, we can look at our plywood sheathing from floor framing and ceiling framing, et cetera. We can, we have all of those metrics and analysis. So you're not just stuck with an acceptance of a day one product.
There are, you can, you can make them wider, you can make them longer, you know, there are things that you can do to adjust them. Uh, and there are rules, there are parameters to that, where if, you know, certain increase in width, it doesn't work. So we're worried that the catalog and the productization and the conversation is a lot more sophisticated and we're just seeing now we have a, we have a, a catalog unit.
Let's say our, our efficiency dwelling unit. We're on project number eight and it's just people like, yep, I want that. Our, we had a mod on the floor, our, um. [00:46:00] Urban One dwelling unit. We truly had, it was in production. We had a developer come in with their team and we said, here, give you a tour of the factory floor.
They stood in it and they said, this is, this is exactly what we want. We said, okay. And we had materials boards in the conference room like a week or two later. And they said, yep, materials are approved. That's just a, it's a whole different level of conversation, meaningful conversation that you're able to have, uh, with all the
different stakeholders and developers.
Evan Troxel: You're really talking about, you know, what, what I think would be classified as informed design, right? It's like you're in your factory is optimized for producing this catalog of modular, you know, volumetric, modular. buildings. And so that then goes into the software, into the rules, into the constraints, with the additional layers now of analysis, environmental noise, and all, daylighting, and carbon, and all these things.
And now [00:47:00] we can optimize it for the site. I wonder if we could just transition back to the actual Project Phoenix site now, Andrew, and you could just kind of tell everybody about it. Because I think one of the things here that, that's important about this story is. And so we're, we're in the process, even though we got to kind of experience some elements of this project before they're actually going to the site at Autodesk University on the expo floor, which was, which was great because it makes it feel real.
But this project isn't, isn't, isn't finished yet. Built yet. You haven't even started construction on it as far as I'm, as I understand it. So maybe you can just talk about the site, like the size of it and what some of the constraints actually are. And then we can maybe wrap up, which is talking about how, how the actual design came together on that site with your pre made these, this catalog of modules, plus the software and the analysis and the back and forth with the city, because another important part of this story [00:48:00] is how you are convincing.
The jurisdiction that, that's gonna oversee this, that like they can trust what you guys are, are proposing to them as well.
Andrew Meagher: So, They said we required the site. About a year before there was a factory. And so I, that was on the developer side. So I left the architecture side, went on the developer side before I then headed up the A& E department. So we, we were in the development office and I was, there I was drawing my little blue boxes next to the orange boxes and coming up with five, six, seven schemes.
Printing them out, Larry Pace pricing them, us getting Charles Salter involved, who's an acoustic consultant, and him opining on some of the configurations, and then us trying to, like, did we fit in enough cars, and that whole thing, back and forth, back and forth. Then there was a pause, because we were really then pivoting to focus on actually opening up the factory and getting that running.
Then, uh, We, we started to re engage, we actually had a couple of different architects look at it from a, you know, more sophisticated design [00:49:00] perspective, and then we involved MBH, and then we involved Autodesk, or, you know, that whole partnership started, and then all of a sudden, we were looking at schemes and options that we could not realize in any other manner.
And. Really arriving. And, you know, there were hundreds of schemes narrowed down to, I want to say maybe a dozen, then narrowed down to six. And then we landed on the one that we all agreed was in the right direction. And each one of those was having feedback from all of us is like, Oh, we want to make this adjustment for this reason where, you know, eventually we're going to want to add a roof deck here or not, or, you know, more.
Uh, balconies at grade, that whole thing. And so we, we went back and forth before we arrived at something. We said, yeah, this is truly going to work because one of our other goals is we have a, a smaller project or smaller effort product. It's 11 dwelling units. It's our most cost effective. It's a three story [00:50:00] project, um, that meets all the building code requirements and really does optimize for habitability while it, uh, uh, minimizes waste.
So we're not just. providing mods, we're able to provide a whole entire structure. We call it Moonshot, our whole, a whole entire building where we understand the concrete footing all the way up, all of those different costs. And if we put those on the site, what does that do to the site? And are we still going to achieve the unit count and the unit mix that we're after?
And the answer is with Autodesk's help and MBH's input and everyone's input from uh, Team standpoint, we were able, Tori arrive at a design where we said, that's what we want to build. And so that's
where we're at right today.
Evan Troxel: And how big is that build going to be? Like how many units? What is, what is the makeup of this
Andrew Meagher: So I, I really ought to know my metrics on this. I'm probably gonna be off by a little bit because I'm, it, I think we're at about [00:51:00] 225 to 250 dwelling units. And I, the, the site I'm gonna have to say is probably in the range. I wanna say it's about. 10 acres, but I could be off. It could be a little bit larger than that.
To me, it's, I don't, I don't look at things in terms of square foot anymore. Like we're, we're so focused on these, these other goals of habitability and community and carbon sequestration. Those kinds of metrics are, are immaterial,
you know, in our day to day conversation.
Evan Troxel: Yeah, it just helps to kind of tell the story though, right, of, of the context of, of what you're talking about here, because you, you are going to be manufacturing these modules that are not going to be standalone little dwelling units, right? You, you're building large buildings, like you said, footing to parapet, there's multiple stories, there's lots of adjacencies, there's a lot of things to consider.
Andrew Meagher: So the, the, I'll call it the, well, on the West side, um, We've introduced this bar, and it's a double bar, and it's, uh, five stories, and [00:52:00] so that'll, that'll create the acoustic buffer that will not only work for the site, but will also work for the adjacent neighborhood, the immediate adjacent neighborhood, because there's a, there is a freeway, and there are bar, an elevated, um, rapid transit, um, So that, that acoustics just comes right over day and night.
Uh, so that double bar will work as that buffer. It will also, the orientation also does maximize for daylight to, you know, come across the balance of the site. So the, our smaller three story structures that I'm talking about, of which there are 10, those are not just sitting in the shadow. So we were able to orient those, give a street frontage and a setback, and then work towards having that setback mirror what was happening across the street with the existing homes, so that there really is a language to the street, and not just a
language of our site.
Evan Troxel: And there's another aspect to projects of this scale for sure, and it probably applies to just about any project, but the, the benefits or the impact on the community that [00:53:00] is surrounding it are real, right? And so there's, there's a beyond the property line aspect. And so when you're talking to the AHJ about doing this project there, how, how much of that came into the conversation as well?
Because you're going to
Andrew Meagher: It was, it was, yeah, it's, it was 90%. That's all they, you know, and rightfully so, right? 90 percent of the conversation is exactly that. And if I, if I lived there, that I would be exact asking the exact same questions. It's, it's right to do. You're telling me you're bringing in, you know, 250 homes.
Well, What's my day going to look like?
Evan Troxel: What's, that going to do to
Andrew Meagher: right. What's it going to do to my parking? What's it going to do to the neighborhood? Are you urbanizing it? Are you strengthening it? You know, and also on one of the side streets, there's existing, um, industrial buildings and there's a trapeze school in one of them. There's a maker space in another.
And so rather than just have the residential turn the corner, On the ground floor, we're, we're having maker space, so we're really trying to reflect [00:54:00] and, and work with the adjacent community there, and, and strengthen that, so it's not just a residential dwelling, residential community, because that's what we want to do.
It's trying to be contextual and strengthen everything that's around us. And that's, and that's what all of, all of the conversation is,
revolves around that.
Evan Troxel: And, and maybe David, we can, we can begin to wrap up here, but I, I'm curious from your point of view, uh, going back to the outcome based design and the goals that you set and where the project stands now in relation to those goals, is it meeting your goals? Is it exceeding your goals? Where, where are you seeing that from the research and the optimization and the metric side of things?
Um, uh,
David Benjamin: Um, that's a good question. I mean, in, in general, we have learned so much from this project and including Andrew from, from you and your great insights and, and care about what makes a [00:55:00] good place to live and what makes a good neighbor, what, what will make Phoenix a good neighbor to the other residents of the community?
Um, I was thinking, Andrew, I've heard you say before, like, Every six or nine months, the, the factory is different you've you cause you're always learning and in a way I think we've, um, we've adopted a little bit of that mentality as well. We're continuously learning and I think now Autodesk is in a position to have its software reflect that more, more fluidly than it used to.
So for example, Autodesk Forma has updates all the time. You know, it doesn't need to ship a new CD, you know, that you, you know, update the version in order to do that. So that software is always learning. The analysis is, is always getting better. New features are, are being tweaked and, and added. Um, and [00:56:00] you know, taking a step back things, the, the, the project has been a great success, I think, for us in.
living through the real world frictions of how to take some of the ideas and innovations, especially in the digital world and see how they can actually work out on this real world project. What are some of the things, um, you know, that are maybe too complicated that we thought weren't too complicated?
What are some of the things, um, that we didn't take into account when we started? you know, imagined how this would be used. You know, who are some of the players who, who don't like it or are even maybe sometimes threatened by the new technology or the new ways of doing things? Um, we learned from, from all of that.
So in that sense, in the, in the sense of this project, we wanted to learn from it and we wanted to get better from it. It's been a huge success. Um, I wanted to mention a [00:57:00] couple of other things because, you know, The project as a whole operated on so many levels for, for us, and I think for, for everyone. So, we were certainly interested in improving and applying our outcome based approach.
design software early in the process. How can we make things more efficient, more interactive, give the right data to all the different stakeholders, like you were describing, Andrew and Evan, you were talking about from the community board to all the different people on the design and engineering team and, and that software, you know, is basically at its best, giving everyone just more information to make better decisions.
It's not really. doing things totally for us. It's not replacing people, but it's give, it's basically a good platform for a more inclusive and informed discussion about how the project should be.
Andrew Meagher: Right. It's almost like if you're, if you say, Oh, here, we're going to market a product and here the product is [00:58:00] going to eliminate architects and take the headache out. And you're going to, you know, have this, you know, dollars based outcome as a, as a developer, you'd be completely misunderstanding what the effort is.
And, you know, come back to the very beginning of this, of our conversation. The daunting task that we have in the next 30 years about carbon and population and habitability and sites. This is these, this is tools and information. It's there. More people are going to be using this. It's not going to be taking
away work.
David Benjamin: Yeah, right. Then there's, there's no shortage of, of work to do. That's definitely true. Um, but I, I just wanted to, you know, we've talked a lot about that. Early stage design. And that's been a huge part of our collaboration and work together and something important for Phoenix and important for a lot of other projects around the world.
Um, but we also work together on, on some other things like, you know, how does the data flow? We talked about how it started with, you already had all of this data, [00:59:00] these Revit models for what you knew you were going to build. And then we flowed that into the early stage conceptual design, and then we work together on the right, you know, uh, versions of the, of the conceptual design and schematic design, and then that can flow back and did start to flow back into the more detailed design, including things like facade.
And then that also is starting to flow into stuff on the. on the construction floor, like tracking things, um, you know, looking at, um, you know, any discrepancies, identifying them early, um, you know, basically logging everything. And, and so that's another thing that we wanted to test out and learn from this project is, you know, for this project and for you as FactoryOS, you're, you're really inspiring and unique way to have.
that whole ecosystem there, right, right there on the same [01:00:00] project, right? Like, you, you know, everything about the project from the earliest stages and most general stages to the nuts and bolts and the construction. And so it was a great way for us to track that data flow across the project and, and learn from that.
Um, also, I, I just wanted to mention, and this is, A little bit software, a little bit, you know, the, the physical world, but it also speaks, I think, to the scalability. Yeah, I wanted to return to this, um, 12 unit, um, building that you're kind of
optimizing in a number of ways. And that I think is, is super scalable.
Um, but returning to the idea of the demonstration project or the kind of innovation village, one of the things that, that came up early on from, from factory OS, and we were so thrilled to hear this was let's use this project to go even a little deeper on [01:01:00] that 12 unit building. Let's, you know, we know we're going to have a few of those 12 unit buildings on this site, in addition to the bar building, as you said, but let's take three of those 12 unit buildings.
and do like a real world physical test of, um, as an experiment. So it's as if, you know, a biologist might make three Petri dishes and one is like the control and one has, you know, a slight change and one has another slight change and you're comparing them. In this project, we are having the opportunity through the vision of Factory OS to say, let's build that 12 unit building three times, mainly the same, but changing a couple of things and monitor, you know, what's, what's the better way to do it?
And that version of continuous learning and experimentation, I think was so inspiring. We dug into some of those details. We looked at which things are better for. Embodied carbon and operational [01:02:00] carbon and, and cost and livability in terms of maybe a passive house inspired version or a naturally ventilated version and not just thinking about it in, in theory, but literally, you know, building it in reality and testing it.
And that was also another inspiring thing that we learned from
Andrew Meagher: and to say, you know, that exercise, the, the level of information that went in and the output, we were talking not just about, um, fresh air, but the actual sizes of the windows and the sizes of the windows as they get larger impacted by an acoustic, you know, implication. And if you have a breezeway. Or you don't have a breezeway.
And if you have a breezeway, what that does to the building envelope and the thermal performance and the operational carbon, and what if you have different HVAC systems, so to have three different projects that we're able to digitally test and then build [01:03:00] and then validate and learn, and if we got something right, bring it to the next and truly iterate, uh, very unique opportunity for
all of us,
David Benjamin: Yeah. And, and again, it's. And I think there was, again, a great synergy because, you know, on the factory OS side, you wanted to continuously improve and learn about that 12 unit building. And on the Autodesk side, we wanted to test out our software, you know, beyond just like you're saying, Andrew, beyond just the conceptual design and the kind of stacking of boxes, but like, let's dig in and really understand how the size of the window impacts the comfort in that unit.
And, you know, if we have, you know, two layers of insulation or sound attenuation, what's, what's going to be the impact and how much, how many more, you know, materials do we need to do some of these things and what's the impact on the carbon footprint? So we really dug in in detail too, [01:04:00] and saw that we can get this dual benefit of the software digital world and the, you know, physical made world.
Evan Troxel: And you have this feedback loop built into your system that I think is, thank you for bringing all that up, David, because that, that is a, I think a lot of architects on the design team would, would look at that as a luxury to have a build side team who is so interested in continuous improvement, right? I think there's so many, uh, There's so much baggage in our industry, which is like, this is the way we've always done it.
What do you mean there's a new way to do it? And you're, you said some, I think, scary words, Andrew. Our, our factory is, is different every six to nine months. Projects in architecture world take years to do. And I think architects love a challenge. on their client's behalf, but it's very rare that they're willing to look at their own processes and their own business [01:05:00] models and the evolution that I think projects like this naturally That needs to be part of the conversation as well, because this is a new way of working.
We talked about process change earlier. This is a major process change, and at the same time, we have to address the current challenges of what's going on in the world right now, right? We have to address the shortages, we have to address the environmental challenges, and, and so, in order to do that, these things need to happen at a much more faster pace at a much larger scale.
And so maybe final question slash topic of conversation, but I'm curious because you guys are both coming at this from a different angle, which is, what do you think about business model changes in AEC when it comes to learning about new ways to work, new ways to address these challenges and how important is that?
And there's going to be a lot of, laggards in this field, right? Who are just gonna watch from the [01:06:00] sidelines for probably decades, right? And not make any changes. But for the ones who really want to address this challenge, who are very interested in making change happen, I'm curious what you think about, you know, advice you can give, lessons that you've already learned, um, what are some of the things, I know David, again, I'm gonna steal from something I heard from you before, which was, which was like, we don't, architects want to come in and their unique vision and the unique design challenge that they're willing to, that they want to solve in a very special way.
We're not talking about that necessarily with this kind of delivery and at the speed and at the scale, like, of course, there's still going to be elements that are special and design and really important. Like design is also function, right? It's not just the aesthetics. Uh, you talk about livability a lot, right?
So all of that, I think, still plays into this. But. But at this, at the scale that this needs to be addressed with existing building, building, uh, business models that are, are going to be kind of, you know, we're, we're going [01:07:00] to, we're going to hang onto those as long as we possibly can. Like, just talk about the mindset shift.
Talk about the, the opportunity here and the challenge.
Andrew Meagher: So I can speak to that pretty thoroughly, I think, in that I've been with the factory since we started and what I'm seeing from an industry perspective is number one, you don't come to the factory unless you already have that innovative mindset. You don't come reluctantly, you come with enthusiasm and validation.
And I'm talking about, you know, from the developer side, developers looking at this. Getting a tour of the factory and going, okay, this is what we want to do. Shortens my construction schedule, brings down my costs. I like the level of spec and finish. They get their architect involved in, I'm happy to say that most of the, gosh, if not all of them that we, that we architects that we work with are excited by the prospect and they're excited about engaging because one of the things we don't do, for example, is take away control.
We're there to [01:08:00] assist and we're there to really get the developer and the architect. the building that they want to have. And so, you know, how, how can we use our tools to get there? Um, So, there's a lot of enthusiasm, a lot of excitement, and the tools are getting easier and more intuitive to use. So, you know, younger architects are absolutely embracing this.
We're able to even build smaller and smaller projects than we ever thought. 50 mods used to be our lower limit of to what we could do in the factory before it just blew us up. Then we got that down, that number was then became 35. We now have two projects. There are mods using catalog, uh, elements in catalog studios that we're interfacing with outside architects and developers and owners and really coming up with inspiring architecture.
So it's, it's been, that hasn't been our roadblock.
Evan Troxel: Nice.
David Benjamin: I would just, yeah, to build on that, [01:09:00] say, um, I, I think there's, there's actually great opportunity here. So, one of the ways is that I, I think probably many architects know a version of this statistic and probably complain about it that, you know, a huge proportion of buildings that get made Um, don't involve hiring an architecture firm. Um, and so all of a sudden, here's a moment and a need and some technology that could allow for architecture firms to start claiming a little more of that proportion of projects that don't normally, You know, involve hiring an architecture firm. So rather than looking at the way things have been done, always been done and complaining about [01:10:00] and fighting over those 5 percent of buildings that are always going to hire an architecture firm, um, and competing with each other and being proprietary and closed and cold up, you know, hold off in your own world, you know, why not, you know, use this kind of reusable design intelligence, the things you already know, leveraged by some new technology and software, and start making yourself valuable to that 95 percent of, of buildings that wouldn't, wouldn't normally, you know, hire an architect.
I think that's a huge opportunity. It doesn't mean a diminishment in value or creativity. I think it's, it could be many things. And so it's. I think that's a great, a great place to go for, for, for new business models and new opportunities for architecture
Andrew Meagher: actually, even if I can speak a little bit more to it, we've all been there where you do a great design and then the, you know, [01:11:00] general contractor comes along and says, you can't afford it. And so then it gets VE'd and then you design it again, and then it might get VE'd. And then during construction, the subcontractor says, Oh, we can't do it that way.
And whatever it is. And so every step of the way is this fear and fairly real that what you envisioned, isn't going to be the final product. With what we're able to do now to having that higher degree of certainty, earlier on means if you have a design idea, it is going to make it across the finish line.
And rather than designing something that never gets built or designing something that you have to not go down that block anymore, because you, you can't, you can't, you can't look at it because it, your, your vision was never realized. We're, we're bringing a lot higher degree of certainty to bringing a
vision to fruition.
Evan Troxel: Yeah, that's a, that's a fantastic point. I've been through that VE process many times and it is painful, [01:12:00] absolutely painful. And to avoid that, right, which I think you're speaking to, to have the certainty up front in the data. And, you know, you, you can quantify these things in a much, Architects have, have rarely been in a position to be able to do that effectively.
A lot of times there, there may be one person on staff. There's probably an outside consultant. And then of course, there's a different spreadsheet, which lives in the contractor's world, which is, it's opaque, right? We don't know what's really driving those things. And so again, all of these kind of speak to the distrust in the system, but for you, for us to be able to have these.
That reassurance earlier on, I think really does kind of, it enhances the quality of the entire project, not just in the outcome, but also in the, the process that we go through to get there. And it isn't, there isn't that fear at every step of the way that this, this is going to get hacked. Right.
Andrew Meagher: You know, I,
yeah, go ahead, David.
David Benjamin: well, I just, um, speaking about potential for, for value [01:13:00] engineering, um, I wanted to, I wanted to just bring up one other quick thing. One of my favorite parts of the project where I, I learned so much, I think, from. From you, Andrew, and from Factory OS, which was about the facade. So the facade, I think, is, is an area where, you know, a lot of architects focus creative energy for good reason.
Um, often there's a lot of value engineering. And we, we add this, um, approach where, Andrew, I learned from you about the, the challenge of, you know, uh, building in a modular way. but then making the facade. And then together we, we explored some other kind of creative opportunities. So I wonder if you, if we could, Evan, if it's okay, just cover that really quickly.
Cause it's a great, another great example of like how we're doing a lot, but there's still so much to be done. And then [01:14:00] here, here was another area
Andrew Meagher: right. This was an area that I, this was on the mod that was in Las Vegas. This is one of the things that I think we're all so proud of is, A key facet, right? We build the mod, we build the volume here in the factory, it ships to site, and you've shortened the construction schedule. That's fantastic.
Once the mods are there, they all have to be stitched together with plywood and metal straps and hold down plates. Then you have to put a layer of dense glass sheathing on the building envelope, tying that all together from a fire perspective. Then you have to put waterproofing on it, and then you have to have your facade go over that.
All of that, your whole modular, innovative effort. Well, the day the last mod is set, all of that innovation comes practically to a screeching halt and you're back to a conventional construction technology iteration with all the risks and challenges that go with that, from weather delays and scaffolding that has to go up and the scaffolding is there so you can't do the landscape in parallel, so everything slows down.
And it was clear to us, [01:15:00] if we could get a facade panel integrated into the mod here in the factory. Or a facade panel that was designed in conjunction with the mods. So after the mods were set, this then came right on the heels of it. And if it could perform some or all of those tasks, could it do this structural stitching?
Could it provide fireproofing? Could it improve acoustics? Could it reduce the waterproofing? If we could do those things, where. actually bringing down the carbon footprint, right? We're not just VEing where, right, it's, it's V, end result. Yes. It's VE if you want to look at, you know, yeah, it's value adding.
Right. So we're, we're, you know, so that's the Holy grail. And we presented that to David Benjamin and his team. And we said, that's what we see. And so he initiated the, the team initiated this collaborative process that really has evolved over the last several years of what might that need to look like?
What, what are its properties? And so we're very [01:16:00] much in the throes of that, but mission accomplished. This is just our iterative. That's how we are. We crawl, walk, run, right? We're very conservative that way. We don't want to just leap to the end and be this great company with promising everything. So step one is we're going to make a panel and we're going to treat it like a rain screen.
And can we get it on the, building and can it perform just, um, you know, the, the minimal work that a facade panel needs to do. And can it do it in an interesting and aesthetically pleasing manner? And we, we did that. Like we could, you could, you could do a building and put this panel on it and it would work.
But that's for us as step one, we have all these other goals that we now know that we have data and testing that we, you know, the next year we'll be improving
upon that. And, that's been, I just, that's been, that's when we opened the factory, this
was not in our horizon. It wasn't there. this is something that came. Did I, did I?
Evan Troxel: one wasn't on the, [01:17:00] wasn't on the bingo
card. Yeah.
David Benjamin: yeah. And, and it was just, it was so influential. Fun to work on that aspect, you know, with, with you, Andrew, um, it evolved over time and we were all kind of experimenting with new ideas, like, but new big picture ideas, but also down to the detailing of the attachments and what were the sizes and how are they going to work.
And, um, but, but to me, you know, maybe to come full circle, it was a small step, but I think a good example in. Not just improving through efficiency, but improving through a new way of doing things. So, you know, my paraphrasing of what Andrew taught me, it was like, you know, normally, you know, you do, you have all these benefits from the prefabricated modular construction, but then you get to the site and you're back to traditional construction for, for a number of reasons.
And could we create a new [01:18:00] system? In this case, like. Basically, 38 ft long panel that has all these five layers of performance, uh, that, that is, are needed for any facade, but also has a very low carbon score because it involves, um, some basically plant based material that has absorbed carbon as it, as it grew, um, and that can have some aesthetics to it.
So you get a totally new. system installed in a new way that helps you with the cost because you can install it really quickly or in the factory. Um, it helps with the carbon because you have this new biomaterial layer. Um, and it also unlocks some new possibilities for aesthetics. so we're not just in the game of like, you know, trade, trade a little bit here, lose a little bit there or incremental, you know, 5 percent efficiency. We're exploring a new system, that might have some [01:19:00] advantages across the board. And reusable innovation from this project. Also obviously driven by a lot of data.
simulation analysis. And that's, you know, part of our, our interest over here at
Andrew Meagher: And that's, that's actually also why other vendors and stakeholders, HUD and whatnot, are interested in working with us at the factory, because you can actually get, if you do it on site in a conventional build, you have a data point of one. And then you can cross your fingers and hope that that was a good data point and that it becomes replicable.
When you do it here, we're able to actually study and, you know, using some of the software from Autodesk is, is this HVAC system better than that and why? And what about the operational costs? What about if we reconfigure how the cast iron works in the floor framing? So, just like all of that, now we have this facade panel that we're able to iterate on and truly study and build.
It's one thing to draw. It's completely another [01:20:00] thing to build. And so to have that confidence moving forward is just
critical.
Evan Troxel: Yeah. Well, this has been a fantastic conversation. And for the audience who's listening, who wants to hear more about that panel system that David was speaking about, uh, the facade system, we're going to have another episode. Discussing that more in depth, which is going to be fantastic. I'm really looking forward to that, but I wanted to say thank you to you both for talking so in depth about this project and sharing what your experience has been over the last few years.
And I'm looking forward to this project, actually breaking ground and getting built and seeing it in action and seeing what we learn through that process as well. That the kind of continuous learning. Aspect of this project and what you all have gone through and then telling that story and sharing the details of it I think is absolutely fantastic and it speaks to kind of reaching the goals or trying to reach the goals of Sharing this and inspiring [01:21:00] others to do the same so that we can meet the challenges that are right here in front of us in a meaningful way because We're not going to do it the conventional way.
It's not going to work. So thank you both so much for spending the time with me today. I really appreciate it.
Andrew Meagher: Well, Evan, thank you for, yeah. Thank you for having us. And David, good to see you.
David Benjamin: Always great to talk to you.
Andrew.