110: ‘Throwing a Stone into the Future’, with Melodie Yashar
A conversation with Melodie Yashar.
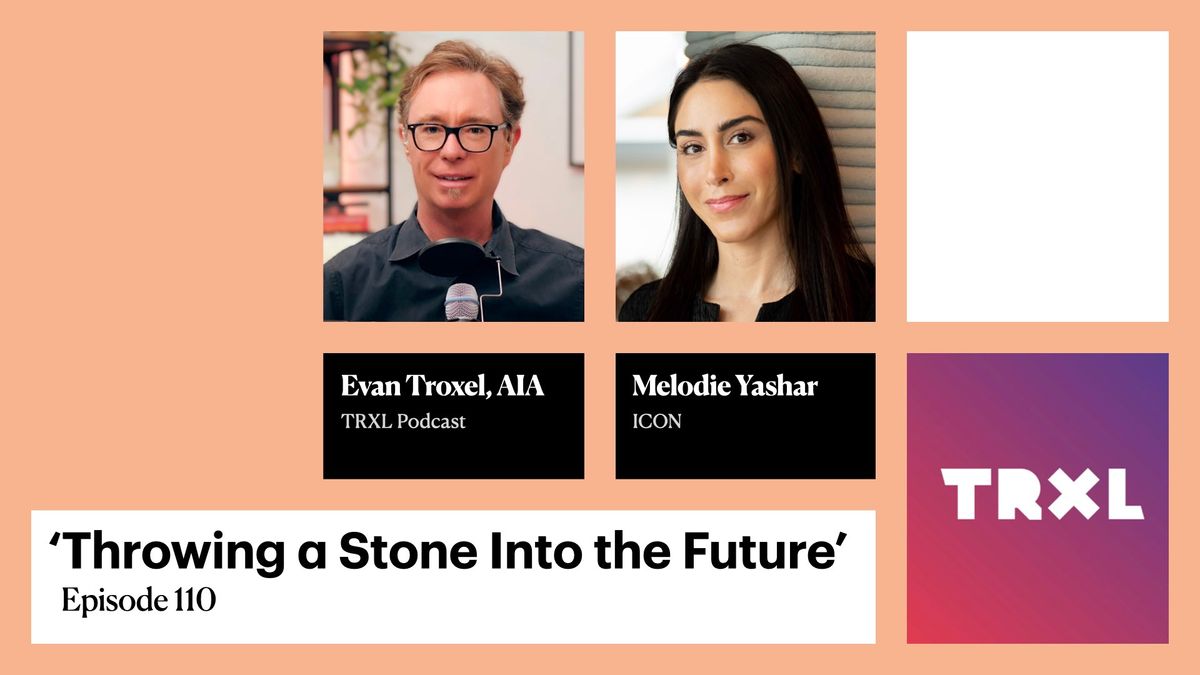
Melodie Yashar of ICON joins the podcast to talk about:
- Earth and Space architecture
- the glacial pace of “traditional” architecture
- her work on competitions for NASA that led becoming a Space Architect
- BIM on Mars
- how she got connected to ICON
- her work at ICON leading the architecture and building performance team
- large gantry-based 3d printing for wall systems
- ICON’s strategic partnerships on 3d printed housing
- procuring building permits for 3d printed housing
- ICON’s upcoming universal housing prototype competition
- and more
Sponsor: TRXL+
- read the announcement
- subscribe to the new TRXL AEC/tech newsletter
- support TRXL directly with membership
- get a special launch discount when you sign up for a year
Latest TRXL AEC/tech Newsletter
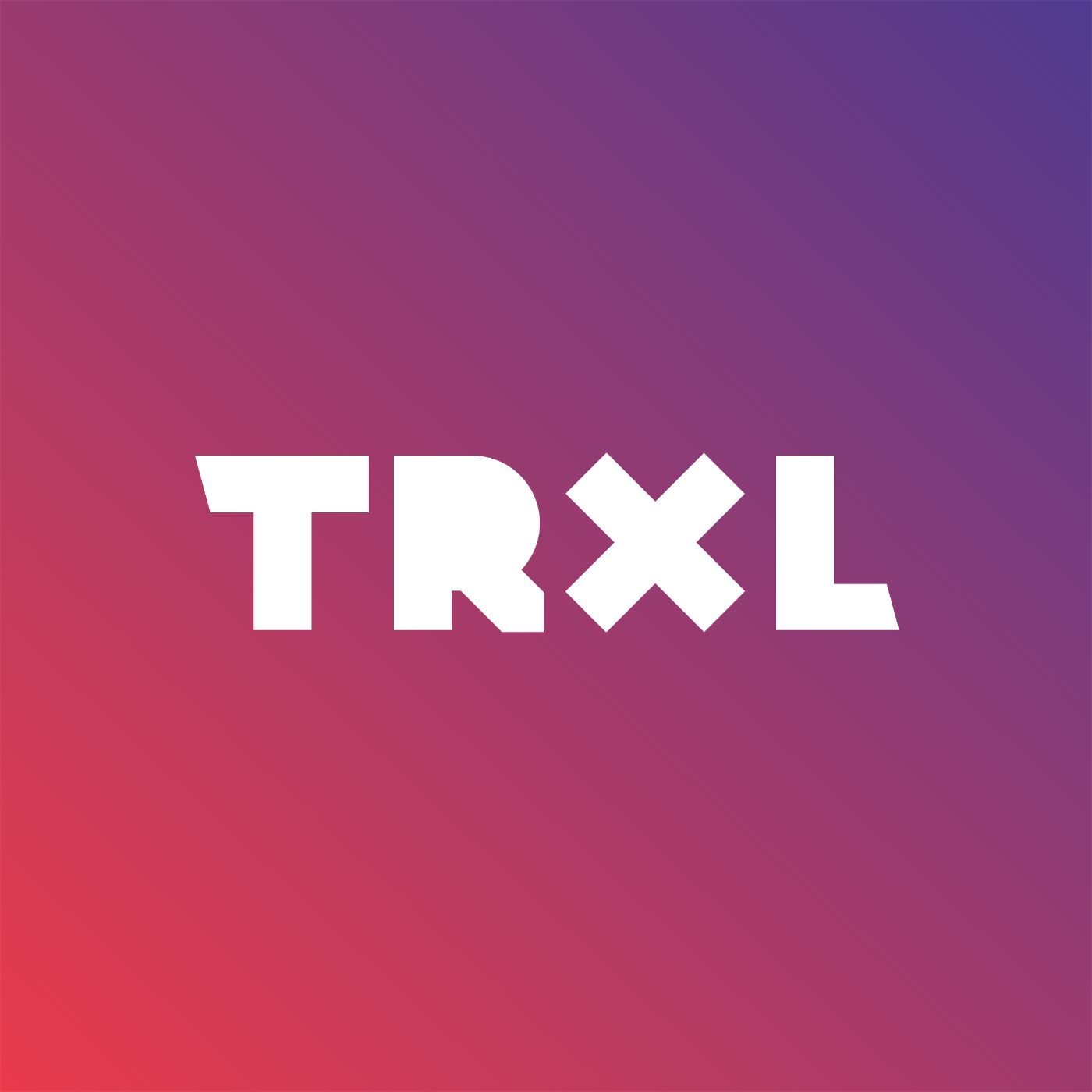
Episode Links
- TRXL+ announcement and limited time membership launch offer
- Melodie on LinkedIn
- Melodie on Twitter
- Melodie on Instagram
- Melodie’s website
- Space Exploration Architecture website
- ICON website
- ICON on LinkedIn
- ICON on Twitter
- ICON on Instagram
- ICON Projects:
- Nadir Calili
- ICON’s Initiative 99: future of affordable housing design competition
Connect with Evan
Watch this episode on YouTube
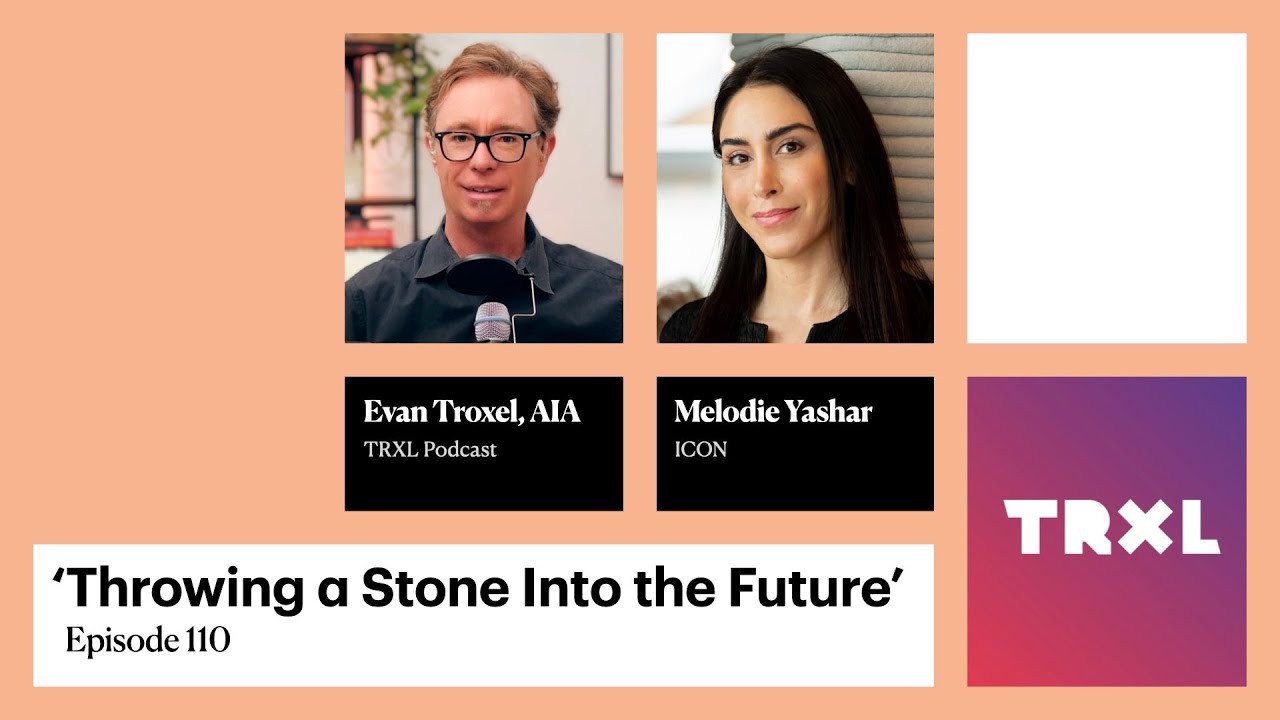
Episode Transcript
110 - ‘Throwing a Stone into the Future’, with Melodie Yashar
===
Evan: [00:00:00] Welcome to the TRXL podcast. I'm Evan Troxel. This is the podcast where I have conversations with guests from the architectural community and beyond to talk about the co-evolution of architecture and technology.
Today I welcome Melodie Yashar. Melodie is a space architect, technologist and researcher. She is the VP of building design and performance at ICON, a construction technologies company focused on large scale additive manufacturing for earth and in space. Melodie oversees the architectural direction of ICON's built work, as well as the performance of ICON's building systems to deliver optimally performing structures that shift the paradigm of home building on earth and beyond. Collaborating across technology and construction teams. Her department supports the design and construction of dignified and resilient terrestrial housing solutions, in addition to supporting the development of ICON's off-world construction systems.
Melodie teaches undergraduate and graduate design [00:01:00] studios at Art Center College of Design. In previous roles, Melodie was a senior research associate with the human systems integration division at NASA Ames via San Jose State University Research Foundation, a co-founder of Space Exploration Architecture, a research group, developing human supporting designs for space exploration, as well as a professor within the architecture department of Pratt Institute. Melodie obtained a master of architecture from Columbia University and a Master of Human Computer Interaction with an emphasis in robotics, from the School of Computer Science at Carnegie Mellon. She geeks out on new material and fabrication technologies. She likes tiny robots. She would like to visit the Moon though not yet Mars in her lifetime.
In this episode, Melodie and I discussed her earth and space architecture, the glacial pace of traditional architecture and Melodie's frustration with that, her work on competitions for NASA that led to her trajectory as a space architect, BIM on Mars, how she got [00:02:00] connected to ICON, her work at ICON leading the Architecture and Building Performance team in 3d printing, ICON's strategic partnership with Lake Flato and Bjarke Ingles Group on 3d printed houses and larger housing developments in Texas and other locations, procuring building permits for 3d printed housing, an upcoming universal housing prototype competition, and more.
So without further ado, I bring you Melodie Yashar. Melodie, thanks for joining me today.
Melodie: Thanks so much, Evan. It's a pleasure to be with you.
Evan: Yeah, this is gonna be great if you were to look back and connect the dots of how you've gotten to where you are now, could you lay that out for the audience?
Melodie: Yeah, absolutely.
I'm the Vice President of Building Design and Performance at ICON. What we do at ICON is develop. Large scale additive manufacturing solutions for both earth and space.
It's a very broad scope of work. My team, the architecture and building performance team, [00:03:00] essentially facilitates all of ICON's, project delivery, and that's for multiple customers in different sectors. And we also do research and development in ICON's, wall systems, developing those wall systems, testing them, acquiring data, and then general building performance and building science, research and inquiries.
The way that I came to ICON, it was actually a pretty natural evolution of events. I had been a co-founder of a firm called Space Exploration Architecture. I like to refer to it as a applied research practice and, Space Exploration Architecture was founded as a result of competing with NASA's centennial challenge for 3D printed habitat on Mars.
That challenge was really focused on delivering design concepts for,, Martian habitats, as well as it identified technologies for 3D printing and outer space. Over the course, of several years, I was introduced to a group at Marshall Space Flight Center that was working with [00:04:00] ICON and they were also our customer, after a while.
And that's how I was introduced to Jason Ballard, who is the CEO of ICON. And, he has a great way of introducing me. He basically was like, well, you have a background in architecture as well as human computer interaction, focusing on robotics and autonomy. Man, have I got a job for you? So he basically brought me on board, and that's how I started the architecture and building performance department and ICON.
Evan: Wow. There's already a few questions floating around in my head. I did get a chance to check out your website, which I'll put a link to in the show notes for the episode, but, Let's go back to like those competitions that you're entering. , because eventually I want to get more into the story of what you're doing at ICON.
When you said Earth and space, it's like how many companies, how many firms out there are there that are playing in those realms? Like you said, it kind of covers this very broad spectrum and so I think we will get there, but let's like the, where the genesis of this whole thing [00:05:00] started, like what drew you to compete in those competitions that you were designing for?
Was it a curiosity about specifically building in space and that this allowed you to do it? Or was it something that came from even earlier?
Melodie: Oh, I love this question. The fact of the matter is that I was working as a, let's say we now refer to it as a terrestrial architect. So I was doing day-to-day architecture in New York for a number of years. , I was extremely underwhelmed , and really frustrated by the amount of coordination and the just general, like, glacial pace in which coordination was happening.
So , I recognize that architecture was not working out for me. There was something that was deeply dissatisfying about, , workflows, both technological software based as well as, The soft skills, the kind of people skills that are relevant to architecture, the position of architects within traditional contracting mechanisms.
Like all of this, felt like it was really ripe for disruption in my opinion. , the [00:06:00] competition actually was something that was done on nights and weekends by myself and a few former colleagues from Columbia University. , we literally did not have any pretenses or ideas that this would become a full-fledged career.
But like we all had day jobs and so we submitted to the NASA competition and didn't really think anything would come from it, but we ended up winning first prize and beating the Europeans face agency as well as foster and partners in multiple other larger bureaucratic firms. So ,there was something there.
And, we started to receive phone calls shortly afterwards and, are , the origins of space exploration architecture in so many words, and it launched a space architecture career and research practice ever since.
Evan: You say there was something there, like , what do you think it was that set you apart from these other huge names in the industry? Was it coming at it from a fresh, new perspective, do you think? Or , what was the differentiator for you guys that if you were to look [00:07:00] back, , is there anything you can pull out?
Melodie: I think we were. A little bit more, let's say. , more aspirational than other groups. We actually knew what NASA's expected answer or solution would be, , because. This is a problem, like the idea of an NC two or let's say a locally produced and manufactured 3D printed structure is something that NASA has been researching and looking into for decades., Um, and the expected answers are out there. The expected answers are use the dirt, which is local to Mars or the moon and establish an equivalency with the way that concrete would typically be manufactured on Earth, and then use that as your building construction material. Concrete's really even in industry, it's the only material that has been demonstrated to, be able to manufacture and construct buildings at scale. Other materials just don't come close in terms of performance. So that was the premise, right? [00:08:00] And we knew that was the premise. And based off of the competition rules and rubric, which. Myself and others, studied very intensely. We specifically generated an idea that deviated from that and yet nonetheless fulfilled all of the competition's main requirements, and rubric, which was based on things like, constructability, aesthetics, bim relevant, so like building information modeling was actually a key. Factor for the scoring rubric within the competition, and other things. It was a research intensive proposal in a way that I think most other, engineering groups or even architectural groups may not have approached it. And yet it came from a place of naivete.
Like we were gathering research from everywhere, planetary, geology, astrophysics, we were totally agnostic to the sources of inspiration and also the research references and consultants that we were bringing aboard. And it [00:09:00] led to this really interesting result. So what we proposed was a habitat made out of water.
We recognized that the search for life on Mars, is going to be tied to the search for subsurface water, ice, which we also have evidence for is like only a few centimeters below the surface of the regoli. And so we thought, well, why not? This is a superior material to regolith or dirt in terms of radiation shielding.
So there's clear value add from a human health perspective, and safety perspective. There's clear value add because in theory you could be within this beautifully translucent and illuminated structure as opposed to being in more or less a dirt based structure. And, and we leaned into that, we leaned into the possibilities of what that could mean architecturally,
Evan: That's a really cool story. I can only imagine. Maybe you can build out what it was like when you heard you won.
Melodie: Um, let's see. It was, uh, the announcement for the phase one competition was made [00:10:00] it was at Maker Fair back when Maker Fair was still happening. So that year was in Queens in New York. And, it was a really cool thing. They announced our team and it was almost kind of cliche, but they had these massive oversized checks to give us.
And so we, like,
Evan: You won the sweepstakes
Melodie: we totally won the sweepstakes. We went up to the podium and Manzi Ramon and others from Centennial Challenges were all there with this massive check. And then we stood behind the check and took a picture and that was how we won the NASA competition in phase one.
Evan: that's so cool. Wow. And so, that was the beginning of the new path because you were saying, you were frustrated with traditional practice and the glacial pace of everything that, in that, right not even like projects, but just. Moving up the corporate ladder, how long does it take , how long do I need to be in this position until I get to the next position, and what do I need to do to get there? And [00:11:00] people don't have answers to these questions. And you know, I think a lot of people can relate to these kinds of feelings.
Right. And so now there's this new path that, is opening up this door that's opening up. And how do you decide to follow it? How do you actually start to commit? I would imagine, I'm guessing here, more of your life to this path than the other path because there's a transition that you maybe sense is coming.
Melodie: Yeah. The fact of the matter is that, it's not like I had a crystal ball to know that this is where it would lead me, but the reality was that the project was so compelling. Mars Ice House, the project, the one was so compelling, it truly spun off and took a life of its own. And the momentum of the project propelled many of us along for the ride.
So what ended up happening is that, a pi from a different NASA center saw the project and was inspired and said, Hey, Let's develop a concept for a [00:12:00] filled and frozen ice habit habitat That led to a two year long research trajectory with multiple rounds of funding.
Evan: What does that mean? Filled and frozen
like molds kind of a thing.
Melodie: basically if you can imagine an inflatable membrane, Instead of it being a 3D printed structure that's robotically constructed, basically the membrane would deploy as an inflatable and you would fill it up just as you would a water balloon, so to speak, and it would freeze.
So that was the concept for Mars Eye's Home. Uh, it ended up being the ICONic project for NASA Langley's Centennial anniversary for the Center. So it got quite a bit of attention. And then again, what ended up happening is that project had so much momentum.
There were synergies developing around the project. It led to the concept for the NASA Big Ideas Challenge, which was, based off of Mars Eye's Home, again, a public solicitation, but this [00:13:00] time to universities asking. Students and universities to think about how to develop a concept of operations for a sustainable Mars greenhouse that leverages the technology as well as the interior programming of Mars ICE's home.
So this kept happening, these projects would have their own momentum and there would be synergies forming by others, folks who are interested in developing concepts further. And the only thing that I can really say in regards to that is it just shows to the power of putting your work out there and letting it be known because it truly does.
It's not just the attention that matters, it's the ideas that people can attach to and relate to, and then hopefully collaborate with you in the future on.
Evan: Yeah. mean, this podcast is kind of an example of that as well, right? It's like once you put something out into the world and it does attract other people who are interested in, you know, going along, figuring [00:14:00] that out along with you, giving you opportunities that nobody knew even existed before.
I can only imagine the pursuit or the path that you were then on with space architecture,? I mean, that is such an interesting thing because it's becoming more and more of a reality in. I guess just from our perception of what's going on out there, seeing the work that ICON is putting on Earth and the different, like you're talking about the different competitions and all these things, there's just more and more of this material marketing material, imagery, ideas floating out there.
I imagine that this is much more of a thing now than it was back when I was in school. Like this wasn't even a concept. It's really interesting to hear the story behind the scenes.
Melodie: Yeah, absolutely. One thing that frustrated me when I was, first getting started, particularly what the competition and the work get following is that so much of these, I'm using the word aspirational, but these [00:15:00] visionary architectural concepts rely on ideas of technology development that don't exist yet.
So you're actually throwing a stone into the future and saying, if this capability's possible, this is what a vision of architecture might be. And I didn't really realize it at the time. It's only now that I can really appreciate it and recognize how powerful that is.
Evan: Mm.
Melodie: Designers and architects in particular are able to set that vision much earlier on for technology development to follow.
And it's been demonstrated again and again, not only in the work that I did with Space Exploration Architecture, but the work that I'm doing now with ICON, and with our current NASA customer and the way in which we have received our funding for our current award supporting development of technologies on the lunar surface.
All of that too, it began with a visionary and schematic concept, which we initiated, not which NASA asked for. So it's [00:16:00] really the design vision. It's really the architecture and really the idea and the concept of living and working in space, which propelled everything forward in terms of the technology development.
So I think architecture is uniquely situated to be able to contribute to those kinds of discourses and set the direction for technology as well.
Evan: It's like watching sci-fi movies from the late sixties and seventies where they were putting these ideas out there and now those are actual things, right? That's the closest analogy I can come up with on the fly here, because it's true that this kind of vision casting, future casting of, technology ways that we communicate through devices, you know, pieces of glass in your hand.
I mean, these are all examples of things that we've seen for the last 40 years, and now here they are. And it's like those ideas shaped reality in the future. I don't see this as being any different than that.
Melodie: Yeah, no, I think you're absolutely [00:17:00] right. The other thing is that a lot of our competitors on the engineering side and the hardware development side, even the software side, are not necessarily thinking about the application of their work, so there's this chasm between design vision versus, the applications of technology.
And more often than not, those technologies are being developed separate from applications. So as far as we can bridge that gap, I think it's going to get us further faster. It's why I always encourage designers and architects to be working hand in hand and collaboratively with engineers as well.
Evan: Mm-hmm. totally makes sense. I, there is another success story that works in the opposite way, which is, I think it was when Steve Jobs announced the iPad, and I'm sure this wasn't a completely true statement, but he said something like, I don't know what you're gonna use it. Show us what you're gonna use this for.
Because they could, you could imagine it being 20 different things, right? It's a newspaper, it's a magazine, it's an email client, it's a web browser. Like it's those [00:18:00] things, but what else could it be? And I think there was some truth in that statement in that, what else could this thing be that we're not thinking of right now?
Because we've been working so hard on getting this device out there. So I do think it can go the other way too, and then it becomes this evolution of collaboration beyond that point, because in some respects, the technologies that we're talking about are developed in secret, right?
Like completely as much as in secret as possible because they're trying to be first, or it's really groundbreaking or, there's any number of reasons there. So anyway, I think that you just can't really, understand when you're doing it, how it's gonna. Turn out in the end.
I'm not trying to downplay the way you explain that at all. I just think that there are other ways in which it happens too. But I do agree about earlier collaboration being better because these different camps, if you will have to understand how the people who are gonna be using it work and the people who are using it have to understand how the people are building it [00:19:00] work to make a truly integrated product that doesn't miss the mark.
It could be software, it could be hardware, it could be whatever. I don't know your experience though, really sounds like you're more on the collaborate early and develop together mindset.
Melodie: I think there's a difference in, the way that we do product and technology development that's specifically targeting consumers versus how we approach what I would consider to be mega projects of human endeavor. And even architecture, like any kind of one-off structure is also a mega project, in my opinion.
So the idea of. Building for the moon and not leveraging architects and not leveraging, folks who are interested in planetary protection or the legal and ethical implications of doing so, that's a missed opportunity. So these mega projects really are intended to be extremely interdisciplinary and collaborative from the start.
At least that's the way that I think they should [00:20:00] be approached.
Evan: Yeah. I've been reading some articles about these. Make a cities, the cities of the future that are like the line and tolosa, and that really speaks to your point well these kinds of cities have to be completely interdisciplinary from the very beginning, otherwise they're gonna be obsolete when they're built.
Melodie: Yeah.
Evan: guess that's one way to say it, but the other way to say it is you just keep building on top of any major metropolis, it is an amazingly organic organism of just continual development all over the place, under places you can't see and it still works, but the kinds of solutions that we're starting to see here are incredibly cross-disciplinary from way before the marketing material hits the internet, it's interesting to think about it that way. It kind of has to be from the start.
Melodie: Yeah.
Evan: So I have one other curiosity here going back to how you got into this. Was it, you know, when you were talking about the frustration with traditional practice [00:21:00] versus this other path, what was it that really drew you to it?
Was it your passion for architecture? Was it space? Was it the research side of it? Was it the technology side of it? Is there any one you can point at, or was it all kind of meshed together?
Melodie: Oh, it was, I was fully convinced that I was leaving architecture and I was done, I was like, I'm finished. The space architecture and applied research that I do with space exploration architecture and in those projects, that's the one exception and it's largely conceptual in nature. So it was, it's something I was extremely passionate in, but I was done with day-to-day coordination when it has to do with building construction.
Evan: Where would you have gone?
Melodie: where would I have gone? , well, I'll tell you what I did and then how I came full circle.
Evan: Okay.
Melodie: I went back to graduate school and, I wanted to pursue a career in aerospace. So I got a second master's. After that master's, I applied for a research grant at NASA [00:22:00] ames via my program.
And then very fortuitously, I received that grant and I was given a full-time offer at NASA ames as well. So I was doing research in a lab that was focused on human systems integration, but particularly looking at the relationship between people and machines and how people interact with autonomous systems.
That was it for me. I was like, this is my trajectory from here on fourth. And the space architecture will just be something that, I take on as passion projects, as they come. And that's it. The thing is, Even though a lot of the low earth orbit commercial space stations have strong customer bases and have good business cases for what they're doing, like planetary applications on Mars, there's not a huge customer base for that yet.
Like, let's be honest. Right? So it's a ways out and I recognize that everybody who I was speaking with, both at NASA and elsewhere was aligned. They were like, let this coast, continue to [00:23:00] develop it and see what happens. But then I met Jason Ballard and then, via our shared customer at NASA Marshall Space Flight Center basically it all came for full circle. And when he offered that I come and start an architecture department at ICON, I recognized it was bridging multiple loves and multiple interests of mine, but doing it from a different perspective. So I was able to rethink the way that construction happens.
We're able to develop our own workflows that make sense for our construction process and for our build process and our technology, and, um even though the typical frustrations that have to do with schedule and timeline and budget that everybody encounters in building construction, those are things that we face as well.
We're just able to do it from a slightly different lens and from a slightly different perspective because number one, we're the technology provider, but also we take full responsibility for design build, which is a very, very different place to be than a designer who's handing, a [00:24:00] project over to a contractor or an owner, as an example.
Evan: Yeah, totally. I had my own design build company with a partner and , I can't echo your sentiments enough where it was like we were designing it, drawing it, and building it, procuring all the materials means and methods, everything. And so, The drawings are different for that kind of a pro , like the whole process is different because it's different, right?
It doesn't have to be the same because you're not handing it off to an entity that you may or may not trust. It was very different there in that scenario. So I totally get that., and I guess just to set a little bit of history here, I'm guessing it's ICON build, right?
Like this is a construction company, but I'm wondering how they were also tied into NASA to tie up this thread here of how you guys came together.
Melodie: Yeah. Yeah. The missing link , what happened next? , essentially as part of the 3D printed habitat competition, NASA was identifying [00:25:00] leading companies, and it also research institutions that represent the state of the art in large scale additive manufacturing. I was actually working with a competitor of ours at the time, and we were very
Evan: we can't name them. Right.
Melodie: I tend not to name, I tend not to name names,
Evan: all right.
Melodie: We were very successful in the 3D printed habitat competition. The thing that was unique about the competition was that it was not only soliciting what they considered to be virtual design, so basically architectural concepts that they were also asking for construction demonstrations as well as testing of those samples and printed specimens.
So, ICON was a finalist in the competition. My prior collaborator was a finalist in the competition, as was I, and that was how we, were able to connect with the Marshall Space Light Center team. And, they have continued relationships with other finalists within the competition as well.
It really was a kind of like accelerator and incubator to [00:26:00] identify who within the large scale additive manufacturing industry overall. So it's been a very successful program and I owe a lot to. Manzi Ramon, who was the program manager for Centennial Challenges. For that, she's really supported my career as well as ICON's career.
Quite extensively.
Evan: So was ICON doing terrestrial projects as well? Other habitable projects before or during the same time they're getting vetted by NASA to possibly produce these on Mars.
Melodie: Yes, yes, exactly. So ICON was co-founded by three individuals, Jason Ballard, Evan Lumis, as well as Alex Laro. And, it was, oh, Some years ago that they produced, the first permitted 3D printed structure in the United States. We also have reason to believe that was the first permitted 3D printed structure in the world. , it was some years ago, and still standing in Austin, Texas. It was [00:27:00] released at South by Southwest. And ever since, every year at South by Southwest ICON has, one up to themselves and we continue to with the new structures, new, experiences and projects to share with the world. But yes, ICON, over the period of the 3D printed habitat competition was doing projects.
For both residential customers as well as for the d o d, and also affordable housing projects. ICON also completed a project in collaboration with New Story Charity, in Naka hookah Mexico, and delivered about, almost a dozen homes within a seismic zone in Mexico.
And, all of those homes are still standing, still occupied and with status 7.4 magnitude earthquake, which was really great.
Evan: 7.4 is no joke. Coming from California. So like you said, it was kind of an incubator of sorts. And so now you guys are off to the races here in the US and I'm sure in other locations as well. Can [00:28:00] you talk about some of the projects that you've been involved with that are really pushing the state of the art in 3D printing?
Melodie: yes, absolutely. I'll mention our largest project today and the one that is, active in construction right now. We're collaborating with Lenar, the home builder on a project in Georgetown, Texas, which is just north of Austin on, 100 home development at a site referred to as Wolf Ranch.
So what we've done is, basically we brought in the BCA Engels group to help us on the design of this project. It was highly intentional to pair what we consider to be one of the greatest world class architects in the world, who would never work with a production scale builder like Lenar on a project that is intended to show economies of scale and the possibilities of additive construction, for development of this size.
So what ended up happening is that Bianca Engels group was able to push [00:29:00] aesthetically what was possible within this development and introduce, a design standard, which, really has not been introduced before within other Lenar projects, residential projects. And yet we're able to leverage the advantages of our construction technology to print faster and, more economically than ever before.
So currently we have seven printers deployed onsite at Wolf Ranch. They're all printing simultaneously. And, some of the, let's say, feedback that we've gotten is that it is the, one of the cleanest construction sites that anybody has ever seen in
Evan: There's no construction waste.
Melodie: Yeah.
Yeah. And, it's really a sight to see these massive gantry printers. Building in parallel along multiple slabs. And yeah, we're planning to have more printers out there at Wolf Ranch fairly soon.
Evan: Can you give us an idea of the scale of these printers? Like you said, it's a big gantry system, I've seen video of these laying down, toothpaste [00:30:00] as it were. But can you just give us an idea of the scale of what you're talking about here? Because I think, people are used to seeing trucks pull up to a job site, and then people crawling all over the project doing all kinds of different things. This is very different than that. And you have this giant machine out on the site. Seven of them give us a clue as to what that's like.
Melodie: Yeah, absolutely. Our current gantry based system we refer to as the Vulcan. It operates on rails. So we essentially have two vertical towers that, operate on Y rails. The rails can be installed and deployed basically infinitely. So there's not really a hard limit to the length of the rails themselves, but there is a limit to the width of the ex beam, which traverses the two towers. That's roughly on the order of 45 feet. So we are looking for lots that are essentially in that range like between 38 and 45 feet. And that is a limit that we have with our current [00:31:00] system, but it has been specifically designed for single family residential typologies. And, that's what the gantry is best suited for is large developments where we are focusing on residential typologies of that scale.
So three to four bedroom homes. And there is also, a height limit currently with our gantry based system, that is 10 and a half feet. But we are actively developing technologies and systems to, surpass that height limit right now.
Evan: what are the constraints with height? I mean, obviously there's this framework that you're dealing with, but does it also have to do with pumping the material up to a certain height? I'm just wondering what the different pieces are that play into that limitation that you have right now?
Melodie: The main constraint is just the fact that the towers are only manufactured to be so high, and the whole system can essentially be, deconstructed and placed into a shipping container for transport. So both the towers, the rails, the [00:32:00] gantry system overall packs into a shipping container.
And also our material handling system is, within a shipping container as well. So that's how we transport and, mobilize the system around from site to site.
Evan: It's not unlike modular, prefab modular or prefab panels or whatever, where it kind of starts at the end in mind and works backwards. I was doing a tour of a prefabricated, a volumetric, modular prefab plant and basically they said at the time, at least that, the design problem starts with logistics of can we get something to the site and then we have to work backwards from there.
Because then you've got all the roads and the bridges and all these different constraints potentially, they at least give you design constraints. It sounds like you have a little bit of that going on with this thing has to be. Sensable, dismantleable packed into a shipping container so they can go somewhere else and do it again.
And this I guess, starts to tie back into what you said earlier about the architecture, [00:33:00] the design team, working with the engineering team hand in hand. I would assume that's what you're doing like there's constraints going both ways there's people who are designing the machine, that does the thing and then there's this output at the end and you've gotta say, well, we've got these size lots that we know we can work with. All of those constraints are kind of a free flowing conversation, I assume, with these different teams , around the table at the same time.
Melodie: Yeah, absolutely. The difference I would advocate for between what we're doing though and offsite construction or anything that relies on transport to site relative to construction, means, and methods and materials, is that because we focus on onsite construction, we're able to create so much more eccentricity and versatility in our structures and designs that you can't really do with modular or prefab or anything that's factory rebuilt and that needs to be flat packed.
So it's true, any robot in a construction, context would need to be deployed and mobilized [00:34:00] somehow. , smaller ones perhaps have a competitive advantage, but given the scale of the structures that we're building, I don't see a better way of doing it, at least not yet. And also it enables so much design freedom to, create curved walls, amorphous and more eccentric geometries.
Again, double curved surfaces, single curved surfaces. These are the really exciting, possibilities that you get with 3D printing as opposed to using traditional steel and wood frame and that type of thing. So why not lean into that, as opposed to having to rely on everything being manufactured in a factory or constructed in a factory and shipped out to site.
Evan: I totally agree. Anybody who has a desktop 3D printer has done exactly what you're talking about, right? It's the first thing you want to try is double curving surfaces that cantilever out over then you start to learn the lessons about support structures and scaffolding and things like that, right?
But, you immediately start to push the limits of what the machine can do, and you start [00:35:00] to try to figure out ways that you have to change your workflow in the model. Case, let's say, to accomplish what you want. You know, like there's all these little tricks. Shrink wrapping the geometry building in little diagonals underneath that you won't really see at the scale of the print and things like, so you can do cantilevers without doing support structures.
And there's all these fun little things that we do as architects too, push the limits. But of course we go right there and I assume it's no different. I was in Austin last November and I was remiss to not have the opportunity to go visit the project that you guys partnered with Lake Plato on, but it has the types of things you're talking about in it, right?
It has, it has these double curving kind of undulating walls. It's a beautiful geometry that's very complimentary to the stick-built roof structure that sits on top of it.
And it just seems like, there's a really nice dialogue there. But you guys made some very. Deliberate decisions to show off exactly what you're talking about, which does set it apart from [00:36:00] a factory built thing or maybe even a site-built thing without, at least, without a lot of effort to form something like that would be incredibly difficult. And labor intensive I'm sure, compared to what you actually ended up with. Could you speak to, that project and just talk about the kinds of things that you guys were going for? Cuz it's, a test piece, kind of a show piece. Obviously it's gorgeous, it photographs beautifully.
Melodie: Yeah, . So how Zero is, the project we completed exactly a year ago, actually, in collaboration with Lake Playdo, our prompt and our brief for the project was designed the most beautiful home that could only be constructed through 3D printing, so optimize the design specifically for 3D printing and what they came up with was a variation on a mid-century modern ranch house. So we have these beautiful Claris story windows, lots of wood contrasting with the robustness and durability of the concrete. And this real [00:37:00] dichotomy between the curved surfaces and geometries that you mentioned, particularly on the facade of the building and then the rectilinearity of the wood and steel and. It's extremely surprising to people when they walk into the home how warm and comforting it feels. I think there's this, misapprehension that concrete is too brutal a material for residential, and we've been able to demonstrate again and again that just isn't the case.
Particularly given how, organic ins sinuous the beads are. Sometimes people love the fact that the beads are not perfectly aligned. Sometimes you get slight bulging and people are really intrigued by , the kind of eccentricities that you get with that sort
Evan: It's, it's organic. Yeah. I, I agree. And just to define the beads that you're talking about, you're talking about the individual layers of the 3D printed wall surface that you're leaving intentionally in this case, on this project exposed. You could go back after the fact and kind of [00:38:00] trel it or maybe during the printing, I don't know what the best way to do it would be, but you could hide that, but you chose to express it.
And I think it really gives the project a texture that you obviously don't normally see. So it, causes maybe somebody to ask questions about it, which is cool. And it also just, you know, the shadow, the light, the way that it plays off of it, the way that it diffuses because it's not a perfectly smooth surface.
All of these things are playing into that warmth that you're talking about.
Melodie: I tend to think so. Yeah. The beads themselves provide an amazing amount of texture. They play off light, just as you said. And, it creates a really interesting environment that you don't typically see in, residential construction at all. It truly does feel like a highly customized build.
And the thing that's so ironic about this technology is that we're able to do this at scale and in an automated way faster, and more affordably than ever before. So [00:39:00] only the printed walls for how Zero. Took about, 10 days, to print the wall system for house zero. And then of course, the rest of the home was finished traditionally, so it took on the order of six to eight months. But what my team is developing actively and research our investigations and how to fully print a 3D printed enclosure. So we're talking both walls continued through, roofings elements as well as, enclosures. And, we're thinking ahead to how we can lean into the possibilities of amorphous geometries again, and more eccentric geometries to create things like domes and arches and vaults as well.
Evan: It seems like a natural path forward. I'm even thinking back, I don't know how familiar you are. With Nader Kelli's work, with Cal Earth and the,
what did he call those? Like super, I can't remember the word
Melodie: Super Adobe.
Evan: Super Adobe. That's it., I was actually involved in one of those projects as a seed [00:40:00] storage building on a college campus in Southern California. It was the first permitted one built. And, it was funny I would like to get into the more practical sides of this, construction type with you if time permits, but it's like the city freaked out about it, right?
They didn't, they didn't know what to do with it. They didn't know how to inspect it. And because of all that, and it was in LA County, they had to have a foundation system that was like three times the size of a typical foundation system and three times the size of anything that Cole had done before.
But that's what it took to actually get it built. And so, the permitting side, like what do these jurisdictions do when you come to them with a project and an opportunity like this? Are they accepting of it or they're obviously risk averse how does that all play out? Because you guys basically are doing r and d in public here at some level. Obviously lots of testing goes into this but there's still of long term hypothesis playing out over time, [00:41:00] right? With these kinds of structures because we haven't had them for a long time.
And at the same time, you can look in other places on earth and you can see buildings built out of dirt that are still standing through the test of time over thousands of years, right? So it's like, it's not that foreign, but at the same time it's not the normal. And so therefore there is risk aversion to that kind of thing.
I'm just wondering what your experience has been on that side, on the practical side of actually getting these things
Melodie: there is no building code that addresses 3D printed construction whatsoever. It just doesn't exist. At least not yet what has happened on the regulatory front is that, the International Code Council Evaluation Service as well as UL, have developed their own appendices specifically for 3D printed construction.
And they've done that in large part because of companies like ICON and other competitors who are really gaining a lot of traction in the market. So we are working to comply with both of those, appendices and standards. We have all of the testing and data relevant to those, [00:42:00] standards. We're also working with them to continue to develop and advance what those standards and appendices are.
Evan: Sure. That's kind of in your best interest. Yeah.
Melodie: Yeah, absolutely. And, they all kind of take precedent from one another. So the Department of Defense has done quite a bit of work with us, and they are developing their unified facilities code specifically for 3D bridge construction , and whenever we do a project with them, there's new things that we learned that go into their UFC code, and it continues to iterate based off of the things that they learned from us and that we learned from them.
There's definitely a call and response goes on there. But in regards to permitting within specific jurisdictions, we have not had much issue, quite frankly, the way that this works is that we, were basically following a provision within. The I bbc, which specifies that if you can demonstrate that alternate means and methods and materials of construction are structurally sound based off the judgment of a building inspector, then [00:43:00] that's sufficient for the building to be permitted.
So, date we've been successful in in Austin and, uh, various other locations in Texas, in Mexico, and in other states. Very soon.
Evan: Cool. As an architect doing traditional buildings, I have this question for you that I'm sure has come up before, but this idea of laying down all these different layers of cement on top of each other, and I would assume you're trying to do what I would consider a continuous print of the walls, right?
So that there's no stopping and curing and then starting up again, and those kinds of things. Is there a cold joint at every single layer of this, and how do you deal with that from a waterproofing? So this is like the total practical architect question, because in traditional concrete construction, cast in place concrete construction, if you do these separate pores, you have to deal with that layer where that happens. So is that happening or how is it [00:44:00] working with waterproofing? with this kind of construction, because I'm sure a lot of people see these and they ask that same question, whereas it's very different from applying a surface to the outside of the building that's continuous after the fact because you're intensely expressing those, right?
Melodie: Yeah. Yeah. That's a great question. So we're extremely conscious of the lift time that goes from layer to layer. There's a balancing act that goes into how we develop the material, how the materials engineered, and then what the radiology of the material is based off of the ambient conditions at the site, but also the size of the print and the time it takes the material to actually flow through the nozzle based off of the size of the structure.
So we're conscious of all of these parameters, and it's something that we're monitoring very closely as we go. So in the off case that there's something out of our control, like it's raining, you know, we're still building out in the wild. We do stop construction and then,[00:45:00] there is a cold joint.
But in any event, we're very conscious of these kinds of, constraints and we do our best, to make sure that what we're building is sound and that we're not going to face any issues later on. Some of what we do like what we're doing at Wolf Ranch is we actually apply a block filler to the exterior of the facade and the wall system. And then customers are able to paint whatever color they would like for the inside of their homes. Architecturally, like folks like Lake Plato, bga, Engels have not been too keen on that direction. They love the exposed quality of the of the material. It's a mortar based cement and, prefer to have it remain that way. Either way it works, it just depends on the customer and the context. We've done some water intrusion testing and we continue to, but, by and large we've been pretty successful with the wall assembly as it's been, engineered and designed.
Evan: Yeah. This like stories of architects being architects is [00:46:00] not surprising. It's reminds me of like the old Frank Lloyd Wright story where there's this house in LA Hollywood called the Holly Hawk house and it's a famous house that he did for, a very famous person and he tilted these walls inside the corridor to her closets, which were massive because she had a huge wardrobe and he tilted all of them because she had an art collection that he didn't like.
Right. So she couldn't hang her art in there cuz it was a natural spot to become a gallery. And he didn't like it. So it's funny because it's like, well, what do the architects want? The wall texture to be inside somebody else's house. Yeah, that's exactly, sounds exactly right. That's funny.
Melodie: That's terrific. I love that.
Evan: where, are you going next? Because you're talking about the research side of things, which is obviously your wheelhouse. So you're talking about domed structures, where you're, morphing wall to roof and I assume other things as well. If I go back in my memory to the images I saw on your website from the competitions, that was a big piece of it too, right?
So give us an idea of [00:47:00] what's happening in the maybe near future of 3D printing.
Melodie: Yeah, we're always looking to. Enhance and improve our capabilities to print virtually any geometry without scaffolding or support material. We have a couple of initiatives supporting, that trajectory. In particular its dos, arches and vaults, and developing both the technology as well as, construction sequencing operations to support how we.
Those specific geometries. So I'm very excited about that. We recently finished a, pavilion, actually. It's a stage and performance area at the Long Center for Performing Arts. It is on the main lawn outside, of the performance center. And it's essentially a public pavilion that will be accessible, actually starting in a few days.
And, the long center will be hosting all of their summer programming there, at least the outdoor programming. And if you take a [00:48:00] look at the project, we're referring to it as the cosmic pavilion. You'll notice the same kinds of undulating surfaces and textures that you would see in the house. Zero facade. But our cantilevering and our overhangs is just slightly more intense . So, we're going a little bit more extreme. And that's just one step in the direction of being able to 3D print full enclosures as well as higher cantilevers and overhangs as well.
Evan: Pavilions are still the forefront of research and technology development and architecture. We've definitely gone through that, that's been, a reoccurring theme.
Melodie: It's very true. The other thing that, I'll note is that we completed an analog habitat, which is basically a research experiment at the Johnson Space Center, and that was our first time 3D printing roof components. So we printed roof panels, lifted and tilted them up using an overhead crane at the Johnson [00:49:00] Space Center, and then installed them on top of the structure.
I haven't really seen anything quite like it, but it was, again, a step in a different direction, thinking about fully 3D printed enclosures rather than just vertical wall systems.
Evan: And I would assume some of the other directions that you're gonna be going is obviously higher, bigger, these are all things that are being figured out as you go along., as far as the next scale of objects that are able to be 3D printed?
Melodie: Yeah, absolutely. We're always looking to improve our construction operations as well, so, we're thinking about how to mobilize faster onsite, how to automate many of the other, construction integration needs that we have. So there's reinforcement within our wall system.
We're looking at, automated reinforcement and inline reinforcement, as something that integrates within our printing process. We're doing the same for many other parts of our construction process, which still [00:50:00] require manual intervention and human intervention generally. So, yeah, it's a very exciting time. Please pay attention to what happens next for ICON.
Evan: That's awesome. Well, is there anything we missed in this conversation that you're just dying to get out there to the audience?
Melodie: I would like to share one final thing. I mentioned previously that ICON had worked on an affordable housing project with New Story in Mexico. We are actually kicking off a global design competition where we're soliciting both architectural firms and professionals as well as university students, to submit to an affordable housing competition that we're calling Initiative 99. We are asking these two groups to help us imagine what the future of affordable housing is by coming up with Universal House. What we're hoping will be a universal housing prototype for under $99,000. [00:51:00] That is just for the construction materials and finish of the house. That does not include the land purchasing or anything else of that nature.
at a point where our technology has matured and our construction operations have matured to the point where this is something that is extremely feasible for us. We can print three homes on a single test bed,, or print bed, I should say.
And we're interested in seeing what are the most. communities, user groups, audiences that need housing and we're hoping, everybody could help us imagine what the future of this program might be. The thing that is a little bit different here is that we are committed and we are promising to print one, if not more, of the winning designs at the end of the design competition.
So in true design build manner, we're going to be working hand in hand with, a number of the selected finalists in the competition to realize their designs, fairly shortly after the competition closes.
Evan: I have to share a [00:52:00] personal story now that you've mentioned this. This is fantastic. And I don't think I've shared this on this podcast before, but when I was in high school, I was in all these r o P drafting classes. It was like a, I forget what that even stands for, regional occupational something.
And it's basically doing the prep work for what I thought was gonna become my architectural career. Turns out it was completely different than what I thought it was gonna be when I actually got into architecture school. But,, we did drafting, we drew residential homes, and I entered a competition. In this r o p community that we had in Southern California where the school that I was at had r o p architectural, another school had r o p construction and I won the competition. And then the r o p construction class built that house. So not unlike what you're talking about, where it's like we're committing to do this and as a high schooler, I can't even tell you what that did to me, right it was incredible. So for those people out there [00:53:00] listening and thinking I could never, like I was, I was a 16 year old kid, like I could never literally, and it happened . So I just want to inspire people out there to look at this and like, you got your start in all of this by entering competitions after hours and doing that kind of thing.
Melodie: Yeah.
Evan: Seriously consider doing that. You never know what's gonna happen. Like you said you thought there was no chance you were gonna win and you won. I thought the exact same thing, so as a high schooler going into architecture school, now that this is not maybe a project that I would put in my portfolio or anything. Knowing what I know now, but still, it was a big deal to say I've drawn a house that got built. That was a big deal to me. I can only imagine, and it doesn't matter how old you are and it doesn't matter what you're doing now, that this could be, a huge opportunity. And so it's really cool to hear that you guys are, it's not just an ideas competition, it's not just the kind of thing where.
take all these [00:54:00] ideas and then use 'em for our own, thing later. No, we're gonna build your idea that you come up with. Obviously there's gonna be a process that happens after the design part of it to actually make it a real thing, but still like, this is a huge opportunity.
It's so cool to hear that. And it just reminded me so, vividly of something that's happened to me in my past that I had to share that because I really want to inspire people to take it on.
Melodie: I love that. That's such a great story too. Desktop 3D printers are so ubiquitous now. Architects and designers don't have access to this technology. I mean, architects and designers don't have access to much construction technology whatsoever. So I'm hoping this competition will really open up that landscape to be thinking about construction technologies in a new way.
And, I really intrigue everybody to take a look at our website. It's initiative 90 nine.com and there will be more information there very soon.
Evan: Cool. I'll definitely put that link in the show notes [00:55:00] and to follow along with you and ICON on social media and the web and Melodie. This has been a fantastic conversation. Thank you for having it with me today.
Melodie: Thanks so much, Evan. It's a pleasure.